Description and operation
MDPS (Motor Dirven Power Steering) system uses an electric motor to assist the steering force and it is an engine operation independent steering system.
MDPS control module controls the motor operation according to information received from the each sensor and CAN (Controller Area Network),
resulting in a more precise and timely control of steering assist than conventional engine-driven hydraulic systems. Components (Steering Angle Sensor, Torque Sensor, Fail-safe relay, etc.) of the MDPS system are located inside the steering column. MDPS unit assembly, steering column, and MDPS unit assembly must not be disassembled for inspection. They must be replaced if necessary.
Components and components location
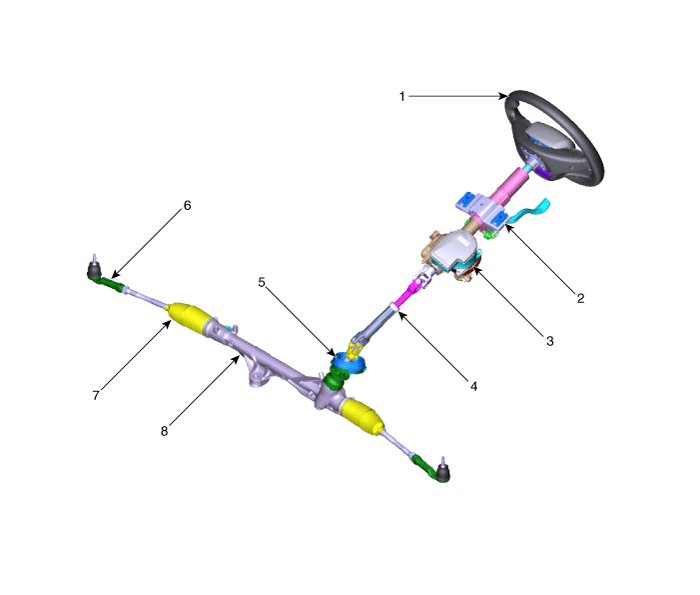
1. Steering wheel 2. Steering column 3. MDPS power pack 4. Universal joint
| 5. Dust cap 6. Tie rod end 7. Bellows 8. Steering gear box
|
Schematic diagrams
C-MDPS
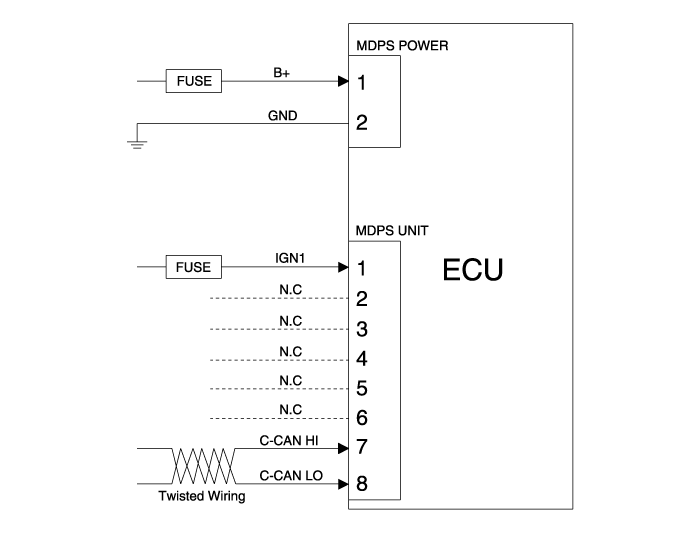
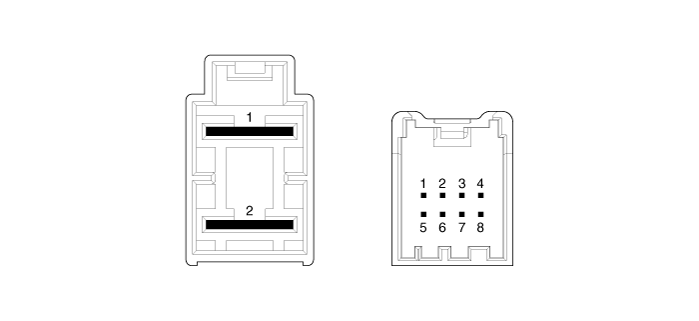
Type
|
Pin No
|
Description
|
Battery
| 1
| Battery +
|
2
| Battery -
|
VSS
| 1
| IGN
|
2
| -
|
3
| -
|
4
| -
|
5
| -
|
6
| -
|
7
| HIGH CAN
|
8
| LOW CAN
|
Repair procedures
MDPS System A/S Workflow
※ For detailed DTC or other DTC A/S procedures, see "CN7 MDPS DTC Diagnostic Guide"
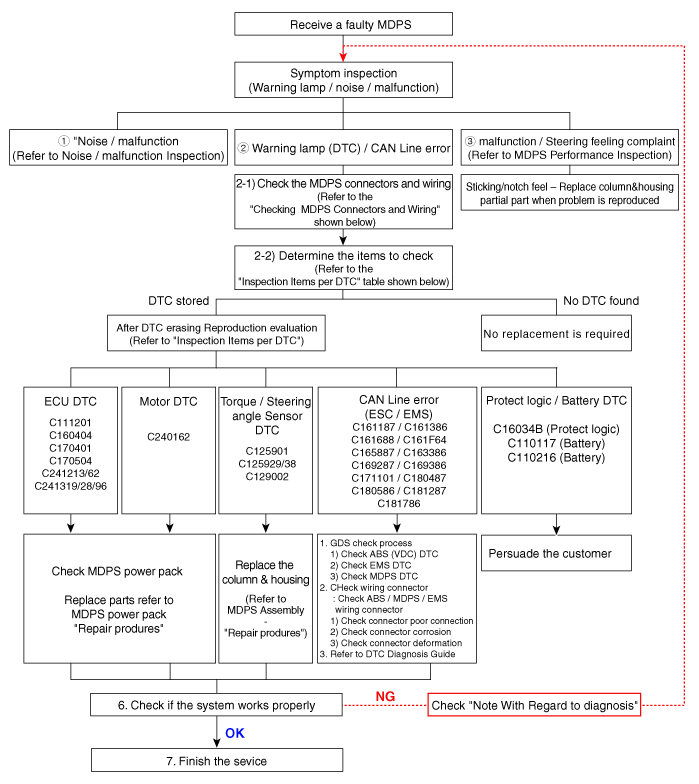
① Noise / malfunction Inspection
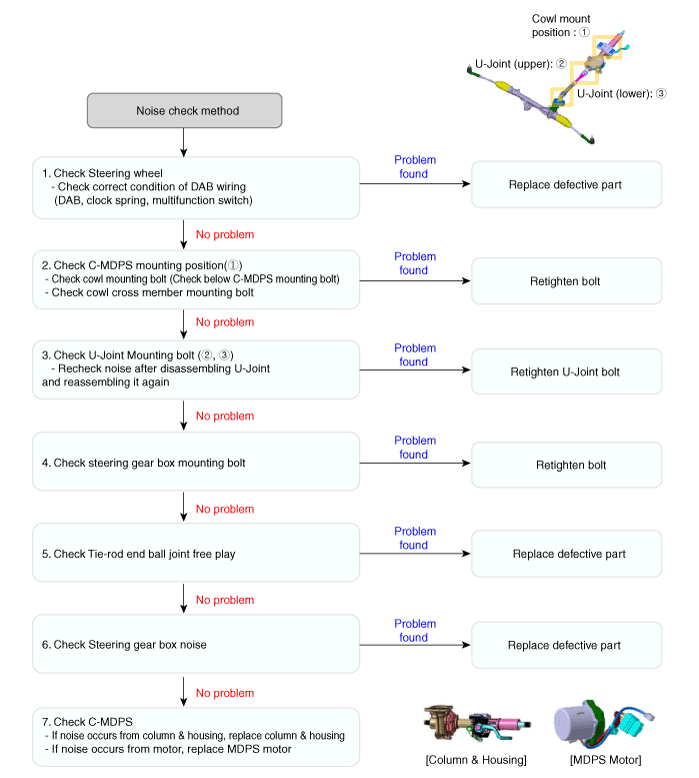
② Warning lamp (DTC) / CAN Line error
2 - 1 Checking Connectors and Wiring
1. | Checking Connectors and Wiring. Check for damage, push-back, or improper connection in each connector and wiring. (1) | Check the wiring on the vehicle side. –
| Check for open / short - circuit due to faulty connection, damage, or foreign substance. 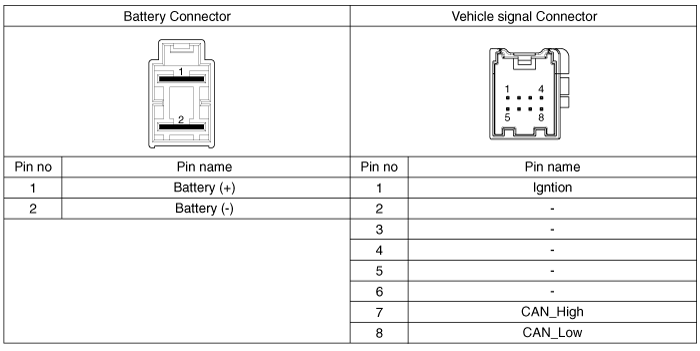
|
|
(2) | Check the motor connector. –
| Terminal Expansion and damage 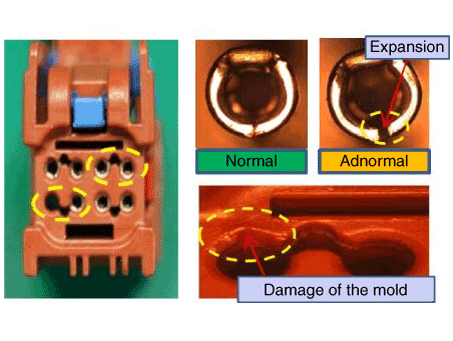
|
•
| Must be replaced the MDPS motor if occur terminal expansion and damage. (Refer to Motor Driven Power Steering - "MDPS Power Pack Assembly") |
|
|
(3) | Remove the grommet (A) and then check the wiring on the TAS side (B) and ECU side (C). –
| Check for damage, push-back, or improper connection in each connector and wiring. 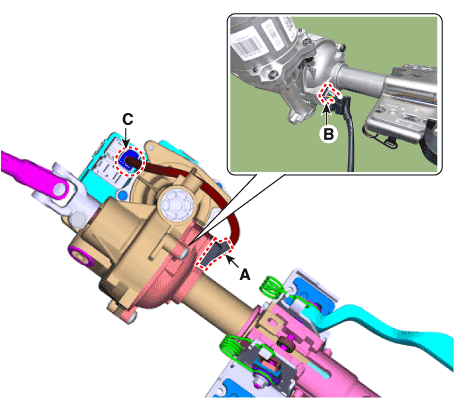
|
•
| For DTC C125901 / C125929 / C125938 / C129002, exchange MDPS wiring. (Refer to Motor Driven Power Steering - "MDPS Wiring") |
•
| If problems are found during the MDPS wiring check, replace the MDPS column & housing. (Refer to Motor Driven Power Steering - "MDPS Column & Housing") |
|
|
|
2 - 2 Inspection Items per DTC
※ For detailed DTC or other DTC A/S procedures, see "CN7 MDPS DTC Diagnostic Guide"
DTC
| Problem
| First analysis method
| How to repair
|
C129002
| Torque sensor signal error
| First erase DTC,
| When the sensor connector flows, the warning lamp reoccurs Replace the sensor cable, and replace the column & housing (56390)
|
check connector connection
|
C125901
| Steering angle signal error
| Earase DTC after resetting Steering angle zero point
|
C125929
| check connector connection
|
C125938
|
|
C111201
| Torque sensor power supply error
| First erase DTC, check connector connection
| When the sensor connector flows, the warning lamp reoccurs Replace the sensor cable, and replace the power pack (56370)
|
C160404
| ECU hardware error
| Check after erasing the DTC
| In case of reoccurrence, replace MDPS power pack (56370)
|
C170401
| Relay breaking of a wire
|
C170504
| ECU over/discharge error
|
C241216
| Motor circuit break / short
|
C241262
| Motor current error
|
C241319
| Over current error
|
C241328
| Motor electric current gate error
|
C241396
| Broken the motor current sensor
|
C240162
| Motor circuit error
|
C126154
| Steering angle zero point error
| Check after resetting Steering angle zero point
| Resetting Steering angle zero point or replace column & housing (56390)
|
Check sensor connector poor connect
|
C161187
| Not received the EMS CAN message
| 1. Check chassis CAN condition
|
|
C161F64
| Vehicle speed monitoring error
| 2. Check connector connection
| Earase DTC (No MDPS replacement)
|
C161F86
| Vehicle speed signal error
| 3. Check engine ECU
|
|
C161688
| CAN BUS OFF
| 4. Start OFF history confirmation message while driving
|
|
C162887
| Not received the cluster CAN signal
| 2. Check cluster connector connection
|
|
C163386
| Cluster display vehicle speed error
|
|
C169287
| Not received the VSM message
| Check ESC, check chassis CAN condition
|
|
C169386
| ESC signal error
|
|
C171101
| ECU abnormal end
| Recheck after erasing the DTC
|
|
C180487
| Cannot be received the LKA message
| Check LKA, check CAN line
|
|
C180586
| LKA signal error
|
|
C181287
| Not received the gateway CAN message
| Check gateway
|
|
C181786
| Gateway CAN signal error
|
|
③ MDPS Performance Inspection
1. | Inspect steering angle and DTCs relevant to the steering system. |
2. | Inspection for heavy steering effort (1) | Inspect tire pressure and width. |
(2) | Check DTCs relevant to the CAN communication error. |
(3) | Check the wheel alignment. |
|
④ MDPS common problems
Case 1
| Case 2
| Case 3
|
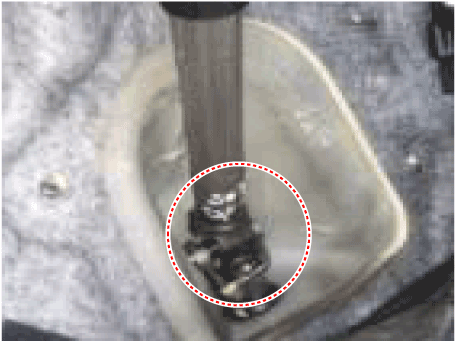
| 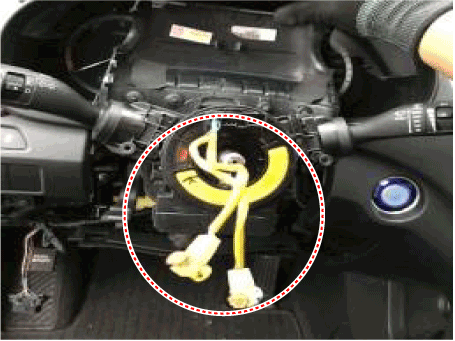
| 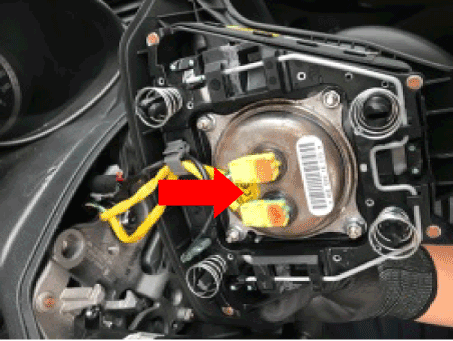
|
Multifunction switch noise
| Clock spring noise
| DAB / Wire noise
|
Retighten the bolt
| Replace clock spring
| Rearrange and replace DAB
|
Case 4
| Case 5
| Case 6
|
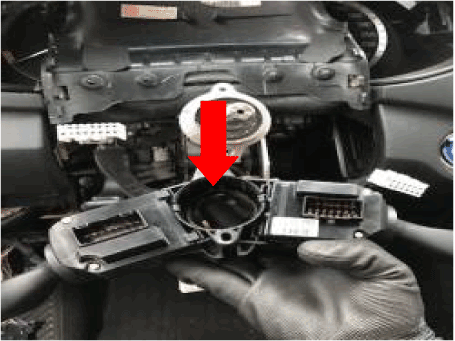
| 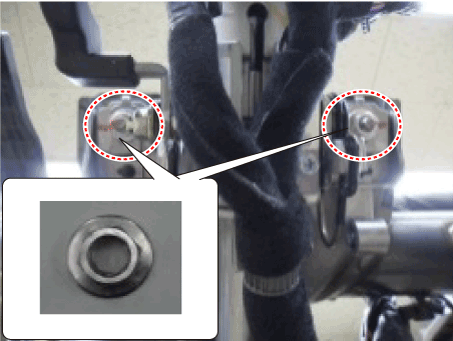
| 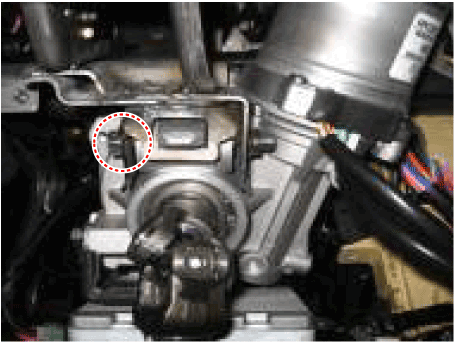
|
Multifunction switch noise
| MB nut mount defect
| M10 nut mount defect
|
Replace multifunction switch
| Retighten nut
| Retighten nut
|
Case 7
| Case 8
|
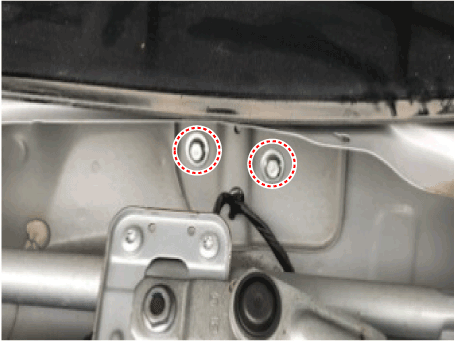
| 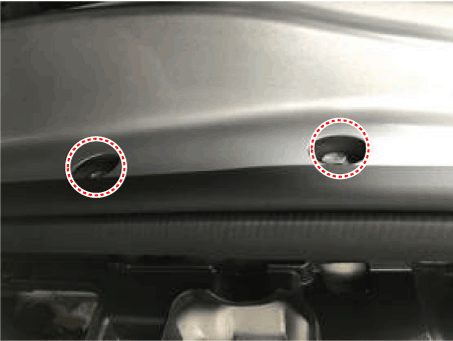
|
Cowl top bolt mount defect
| Cowl bar nut mount defect
|
Retighten cowl top bolt
| Replace clock spring
|
Cautions to be taken when handling the MDPS (Motor Driven Power Steering) •
| Failure occurs due to internal damage because of the drop of and shock and excessive external force on the new partial component. → Be cautious of shock on the partial component and replace the damaged part (due to drop, etc.) with a new one. |
•
| When fastening the steering, excessive impact may result in twisting the center point of the torque sensor. |
•
| When removing/installing the connector the wiring may be damaged (deformed) by excessive external force. |
•
| Be cautious when storing and replacing the partial components under the abnormal temperature and humidity conditions. |
|
MDPS PowerPack Assembly
Repair procedures
1. | Turn the steering wheel so that the front wheels are placed in the straight ahead position. •
| If the steering wheel and the front tires are not set straight ahead together, it may affect the number of circulation of steering wheel and damage the cable inside the clock spring. |
|
|
2. | Turn the ignition switch OFF and disconnect the battery negative (-) cable. •
| Disconnect the battery negative cable from the battery and then wait for at least 3 minutes. |
|
|
3. | Remove driver airbag (DAB) module. (Refer to Restraint - "Driver Airbag (DAB) Module and Clock Spring") |
4. | Remove the steering wheel. (Refer to Steering System - "Steering Wheel") |
5. | Remove the clock spring. (Refer to Restraint - "Driver Airbag (DAB) Module and Clock Spring") |
6. | Remove the steering column shroud panel. (Refer to Body - "Steering Column Shroud Panel") |
7. | Remove the crash pad lower panel. (Refer to Body - "Crash Pad") |
8. | Remove the brake booster. (Only RHD) (Refer to Brake System - "Brake Booster") |
9. | Remove the brake pedal. (Only RHD) (Refer to Brake System - "Brake Pedal") |
10. | Disconnect the MDPS connector (A). 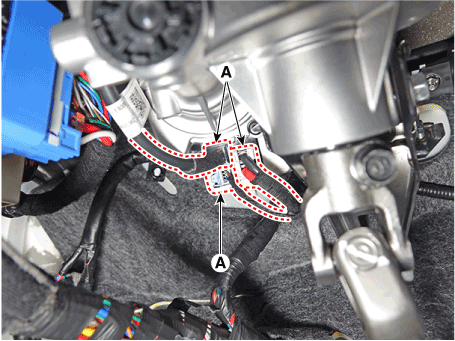
|
11. | Remove the wiring clip (A) from the steering column. 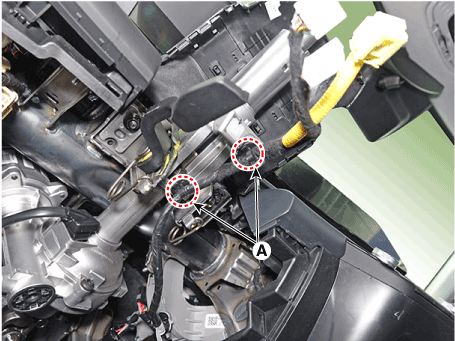
|
12. | Remove the steering column assembly after loosening the mounting nuts (A) and bolt (B). Tightening torque (A) : 25.0 - 29.4 N.m (2.5 - 3.0 kgf.m, 14.5 - 21.7 lb-ft) (B) : 53.9 - 58.8 N.m (5.5 - 6.0 kgf.m, 39.8 - 43.4 lb-ft) |
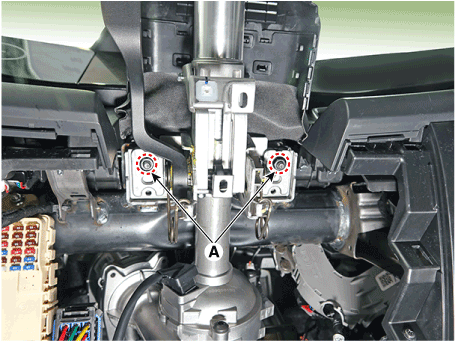
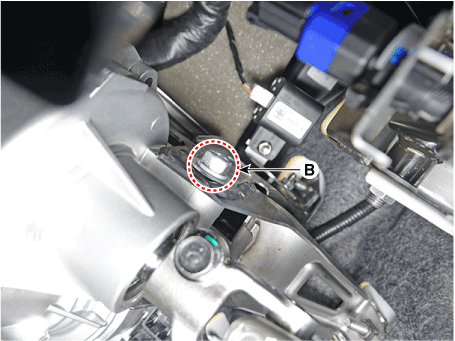
|
13. | Remove the MDPS power pack (A) after loosening the bolts. Tightening torque : 8.0 - 12.0 N.m (0.82 - 1.22 kgf.m, 5.9 - 8.8 lb-ft) |
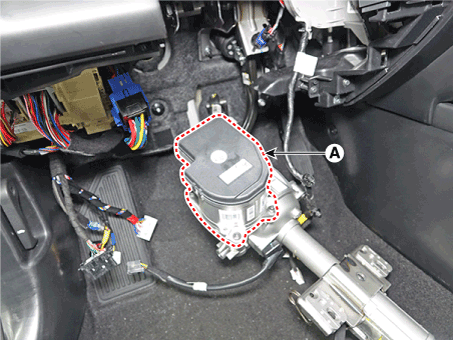
|
14. | Install the new MDPS powerpack. •
| Check the couple ring (A) whether it is assembled, before installing the new MDPS motor. 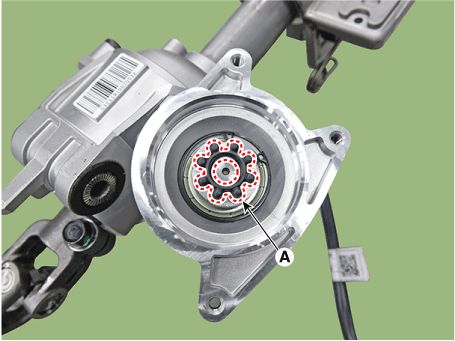
|
|
|
15. | To reassembly, reverse the disassembly procedure. |
16. | Conduct the "EPS Type Recognition" by diagnostic tool. (Refer to MDPS PowerPack Assembly - "Diagnosis with Diagnostic tool") |
17. | Conduct the "ASP Calibration" by diagnostic tool. (Refer to MDPS PowerPack Assembly - "Diagnosis with Diagnostic tool") |
Diagnosis with Diagnostic tool |
•
| When missing the EPS Type Recognition, occure a problem with motor driven power steering performance. |
|
EPS Type Recognition procedures
1. | Connect self-diagnosis connector(16pins) located in the lower of driver side crash pad to self-diagnosis device. |
2. | Turn the self-diagnosis device after key is ON. |
3. | Turn the steering wheel to straight ahead position. |
4. | After Selecting the "vehicle model" and "system", select the "EPS Type Recognition" on diagnostic tool vehicle selection screen. 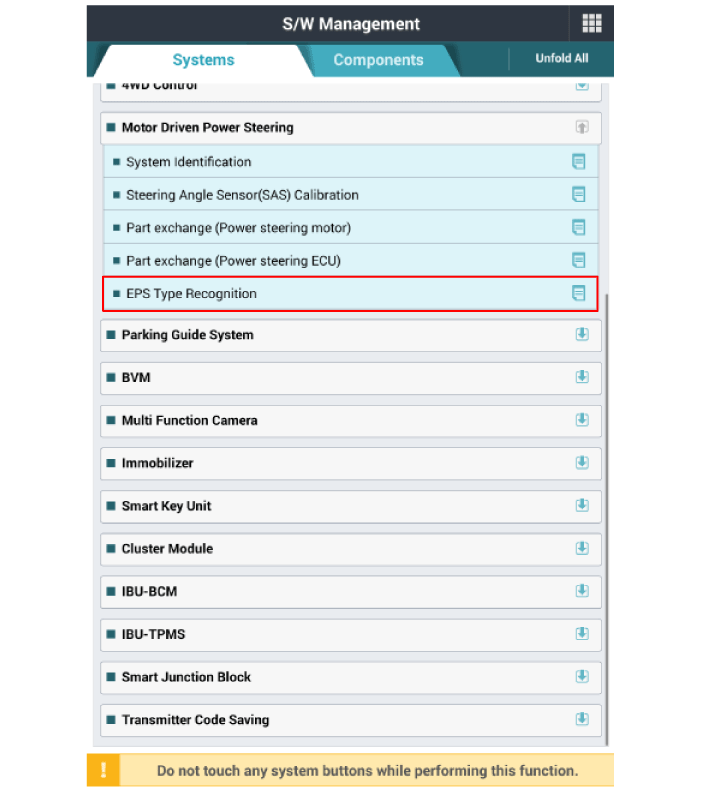
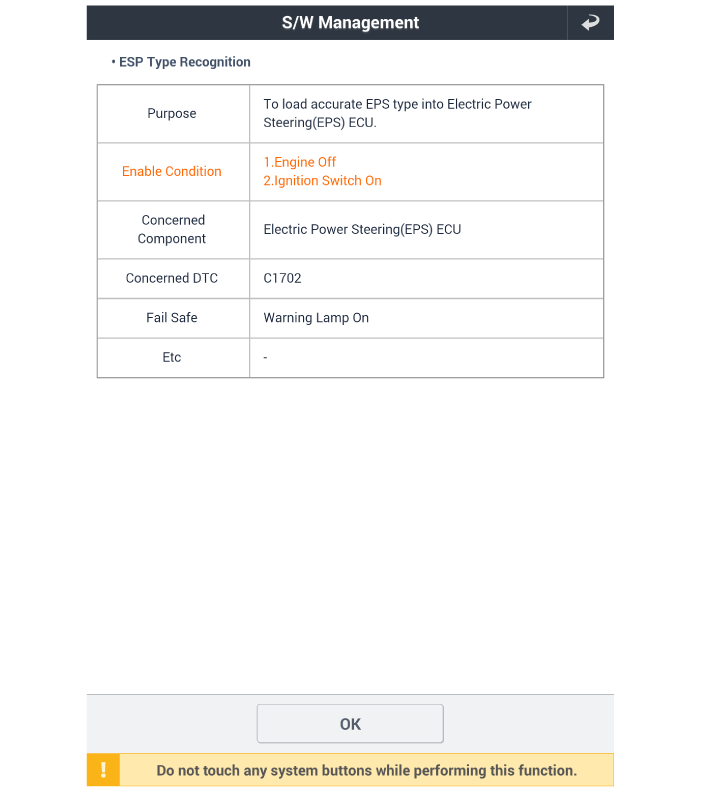
|
6. | Turn off the IG switch and wait for 20 seconds or more before starting the engine. And then make sure that MDPS works properly. SAS Calibration –
| Steering-angle sensor detects the steering angle and steering angle speed. Steering angle and steering angle speed are used for steering wheel damping and return controls in addition to providing assistance torque. |
•
| You can use a scan tool to (diagnostic tool) check if the battery voltage is proper before perform the "SAS Calibration". |
•
| Make sure that no connector engaged to the vehicle or scan tool is disconnected during the "SAS Calibration". |
•
| Once the "SAS Calibration" is complete, turn off the IG switch and wait for 10 seconds or more before starting the engine to check the operation. |
|
|
SAS Calibration procedures
1. | Connect self - diagnosis connector (16pins) located in the lower of driver side crash pad to self - diagnosis device. |
2. | Turn the self - diagnosis device after key is ON. |
3. | Turn the steering wheel to straight ahead position. |
4. | After Selecting the "vehicle model" and "system", select the "SAS Calibration" on diagnostic tool vehicle selection screen. 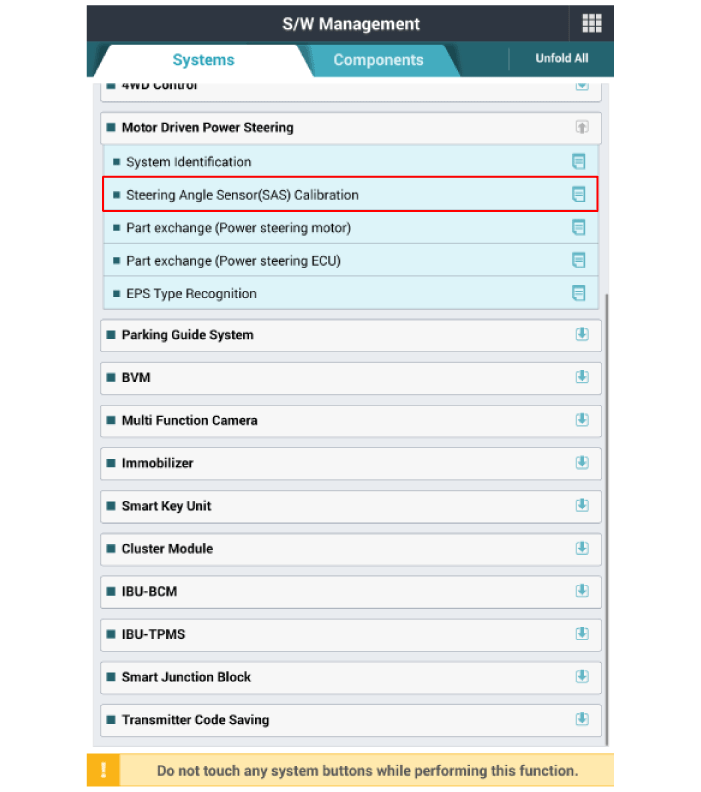
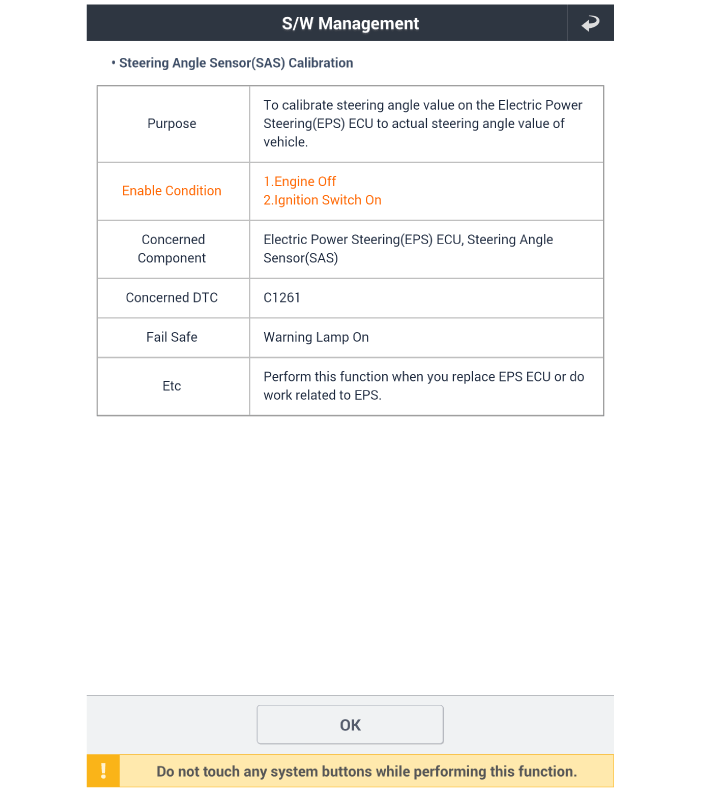
|
6. | Turn off the IG switch and wait for 10 seconds or more before starting the engine. And then make sure that MDPS works properly. |
MDPS Column and Housing
Repair procedures
1. | Turn the steering wheel so that the front wheels are placed in the straight ahead position. •
| If the steering wheel and the front tires are not set straight ahead together, it may affect the number of circulation of steering wheel and damage the cable inside the clock spring. |
|
|
2. | Turn the ignition switch OFF and disconnect the battery negative (-) cable. •
| Disconnect the battery negative cable from the battery and then wait for at least 3 minutes. |
|
|
3. | Remove driver airbag (DAB) module. (Refer to Restraint - "Driver Airbag (DAB) Module and Clock Spring") |
4. | Remove the steering wheel. (Refer to Steering System - "Steering Wheel") |
5. | Remove the clock spring. (Refer to Restraint - "Driver Airbag (DAB) Module and Clock Spring") |
6. | Remove the steering column shroud panel. (Refer to Body - "Steering Column Shroud Panel") |
7. | Remove the crash pad lower panel. (Refer to Body - "Crash Pad") |
8. | Remove the brake booster. (Only RHD) (Refer to Brake System - "Brake Booster") |
9. | Remove the brake pedal. (Only RHD) (Refer to Brake System - "Brake Pedal") |
10. | Disconnect the MDPS connector (A). 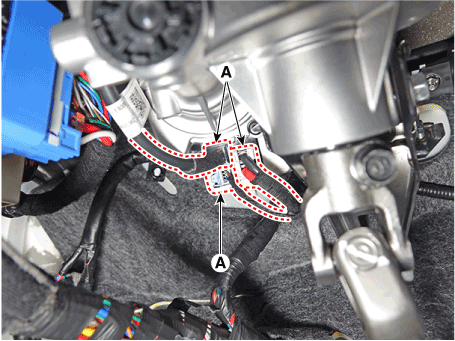
|
11. | Remove the wiring clip (A) from the steering column. 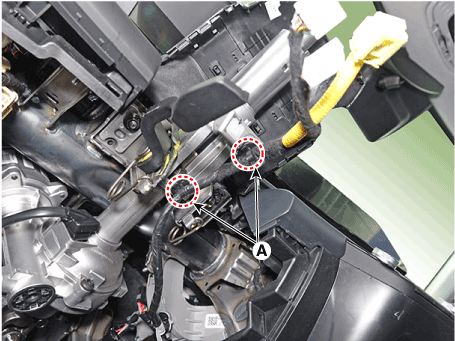
|
12. | Separate the universal joint from the steering gear box after loosening the universal joint mounting bolt (A). Tightening torque : 49.0 - 58.8 N.m (5.0 - 6.0 kgf.m, 36.2 - 43.4 lb-ft) |
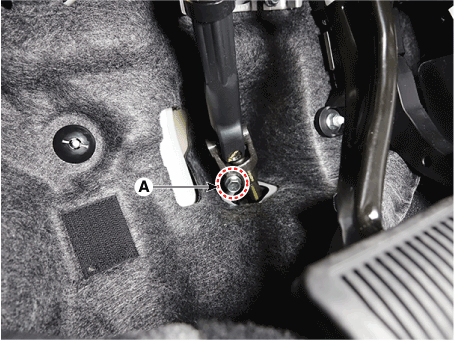
•
| Lock the steering wheel in the straight ahead position to prevent the damage of the clock spring inner cable. |
•
| When mounting, securely insert the universal joint into the steering gear box pinion shaft. |
•
| Do not reuse the universal joint bolt. |
•
| Assemble so that pinion shaft shark pin can be inserted between the joint slots. |
•
| Install by aligning the machining surface (A) of the universal joint and the machining surface (B) of the steering gearbox pinion shaft. 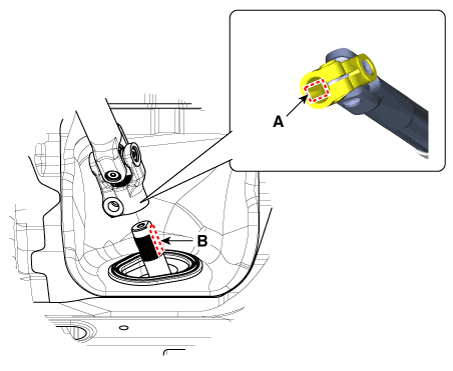
|
|
|
13. | Remove the steering column assembly after loosening the mounting nuts (A) and bolt (B). Tightening torque (A) : 25.0 - 29.4 N.m (2.5 - 3.0 kgf.m, 14.5 - 21.7 lb-ft) (B) : 53.9 - 58.8 N.m (5.5 - 6.0 kgf.m, 39.8 - 43.4 lb-ft) |
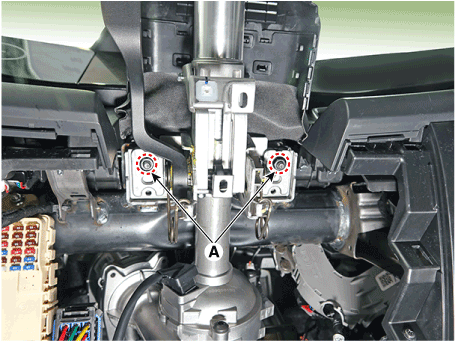
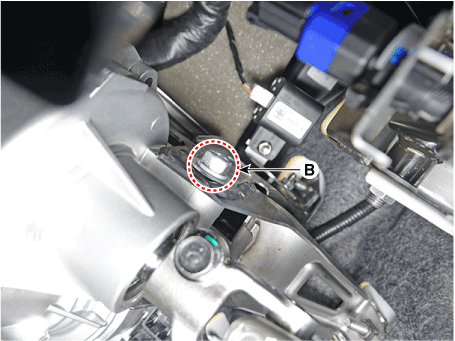
|
14. | Separate the steering column assembly and universal joint assembly after loosening the mounting bolt (A). Tightening torque : 49.0 - 58.8 N.m (5.0 - 6.0 kgf.m, 36.2 - 43.4 lb-ft) |
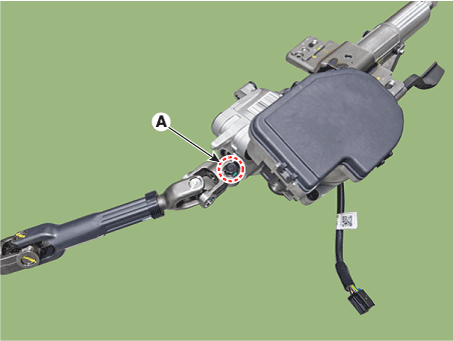
|
15. | Disconnet the grommet (A). 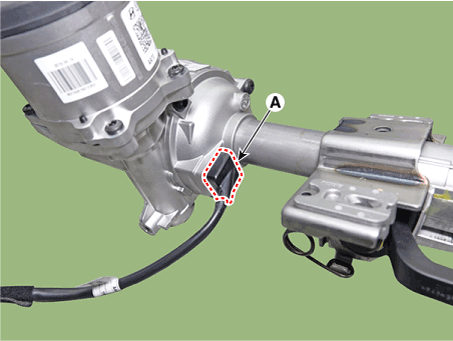
|
16. | Disconnect the MDPS wiring connector (A). 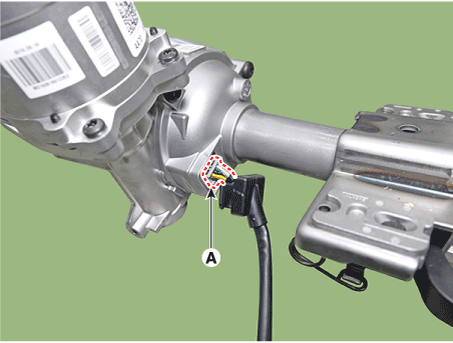
|
17. | Remove the MDPS power pack (A) after loosening the mounting bolts. Tightening torque : 8.0 - 12.0 N.m (0.82 - 1.22 kgf.m, 5.9 - 8.8 lb-ft) |
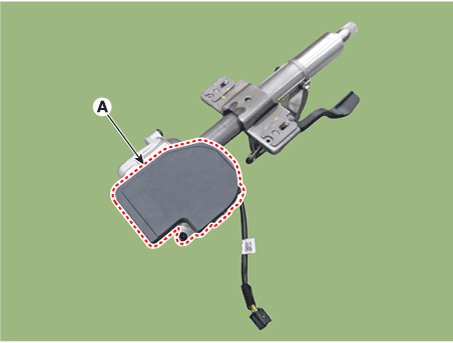
•
| Check the couple ring (A) whether it is assembled, before installing the new MDPS motor. 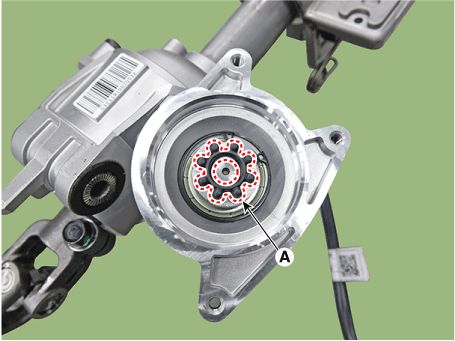
|
|
|
18. | To install, reverse the removal procedures. |
19. | Set the Steering angle zero point by using the diagnostic tool. 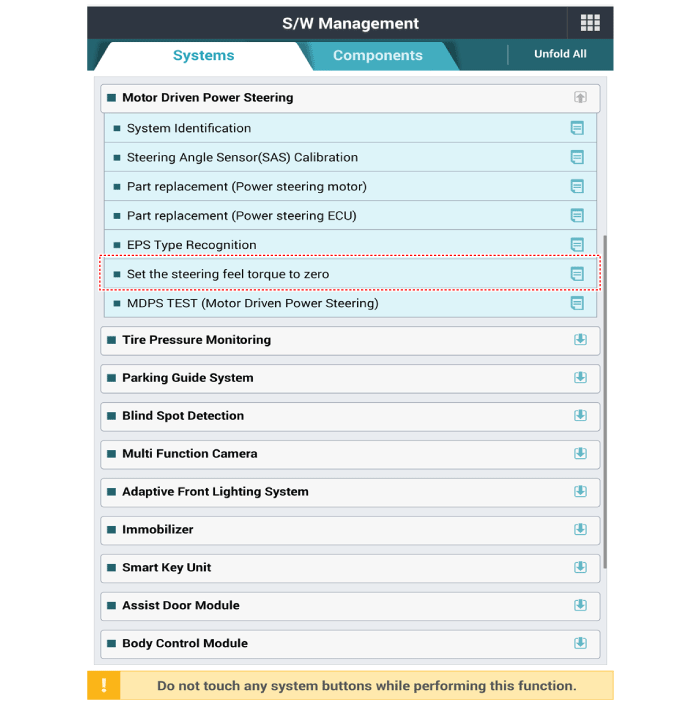
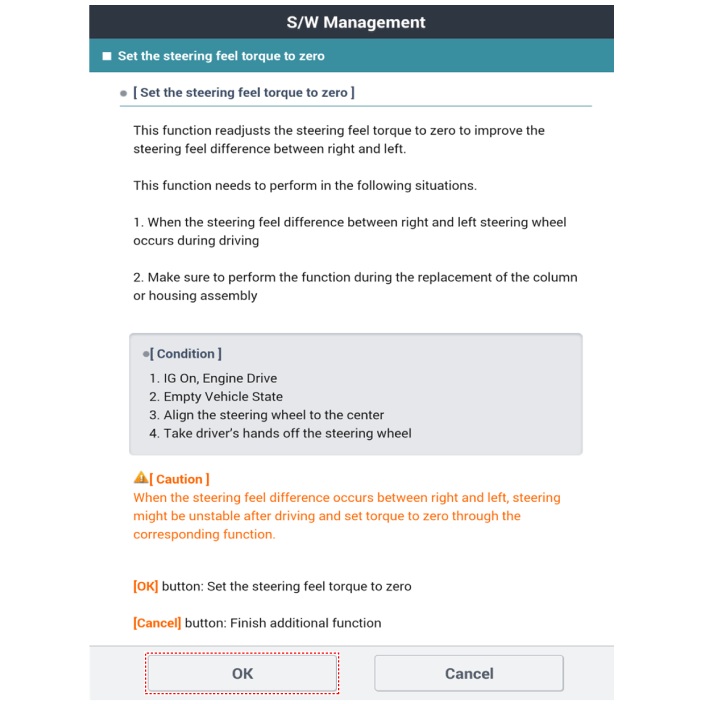
|
20. | Conduct the "EPS Type Recognition" by diagnostic tool. (Refer to MDPS PowerPack Assembly - "Diagnosis with diagnostic tool") |
21. | Conduct the "ASP Calibration" by diagnostic tool. (Refer to MDPS PowerPack Assembly - "Diagnosis with Diagnostic tool") |
22. | Conduct the MDPS Performance Inspection using the diagnostic tool. (Refer to Motor Driven Power Steering - "MDPS Performance Inspection") |
24. | Turn off the IGN switch and wait for 20 seconds or more. Then check the operation after starting the engine. |
Small bearing
1. | Remove the crash pad lower panel. (Refer to Body (Interior and Exterior) - "Crash Pad Lower Pannel") |
2. | Remove the small bearing cover (A). 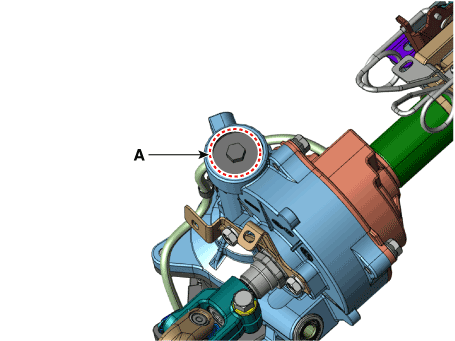
|
3. | Remove the small bearing (A) by rotating in the direction of the arrow after installing the SST (09563-IB000). 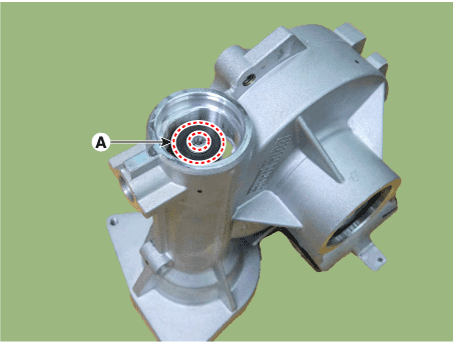
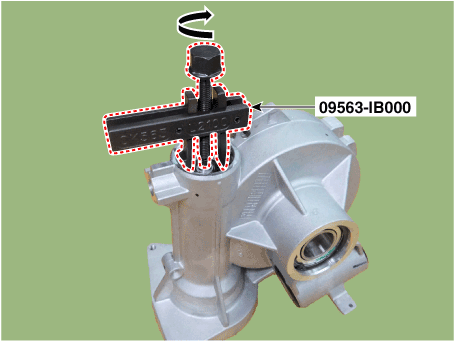
|
4. | Install the new small bearing (A) to the SST (0956-IB200). 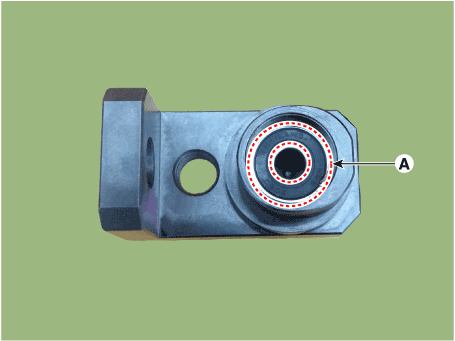
|
5. | Press the small bearing by rotating in the direction of the arrow after installing the SST (09563-IB000). Tightening torque : 2.0 - 2.9 N.m (0.2 - 0.3 kgf.m, 1.4 - 2.2 lb-ft) |
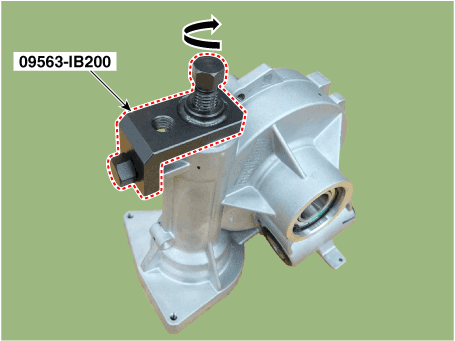
|
Steering Gear Box
Repair procedures
1. | Loosen the wheel nuts slightly. Raise the vehicle, and make sure it is securely supported. |
2. | Remove the front wheel and tire (A) from the front hub. Tightening torque : 107.9 - 127.5 N.m (11.0 - 13.0 kgf.m, 79.6 - 94.0 lb-ft) |
•
| Be careful not to damage the hub bolts when removing the front wheel and tire (A). |
|
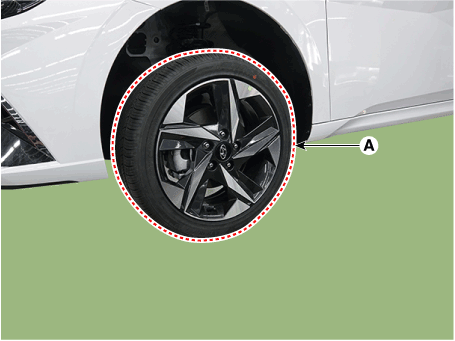
|
3. | Remove stabilizer bar link from the front strut after loosening the mounting nut. Tightening torque : 98.1 - 117.7 N.m (10.0 - 12.0 kgf.m, 72.3 - 86.8 lb-ft) |
•
| When loosening the nut fix the outer hexagon of stabilizer bar link. |
•
| Be careful not to damage the stabilizer link boots. |
|
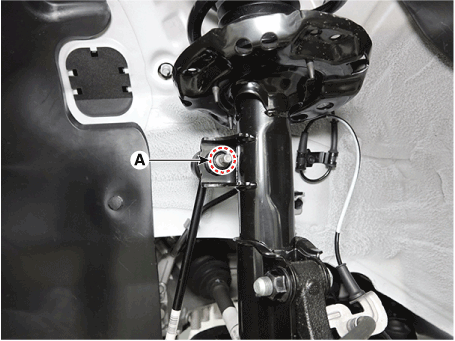
|
4. | Remove the tie rod end ball joint by using the special service tool. (1) | Remove the split pin and castle nut (A). |
(2) | Remove the tie rod end ball joint (B) by using the SST (09568-1S100). Tightening torque : 34.3 - 39.2 N.m (3.5 - 4.5 kgf.m, 25.3 - 28.9 lb-ft) |
•
| Do not resuse castle nut. |
|
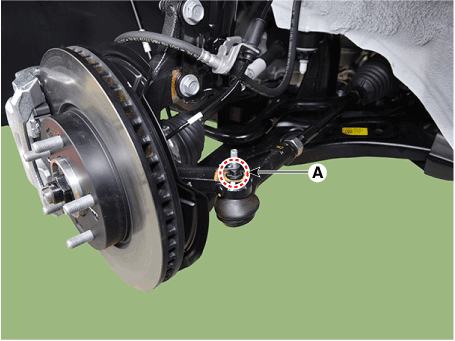
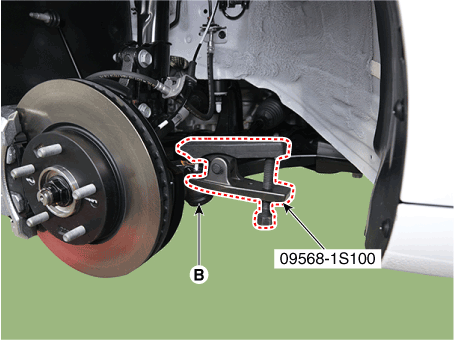
|
|
5. | Separate the lower arm ball joint by using the SST (09568-1S100) after loosening the lower arm mounting nut (A). Tightening torque : 68.6 - 80.4 N.m (7.0 - 8.2 kgf.m, 50.6 - 59.3 lb-ft) |
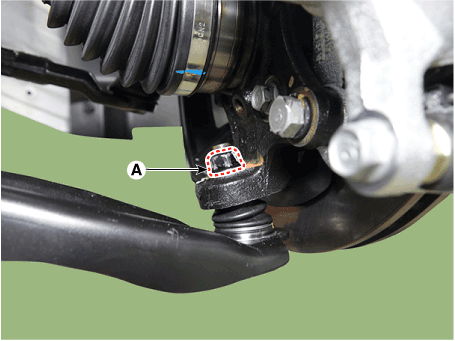
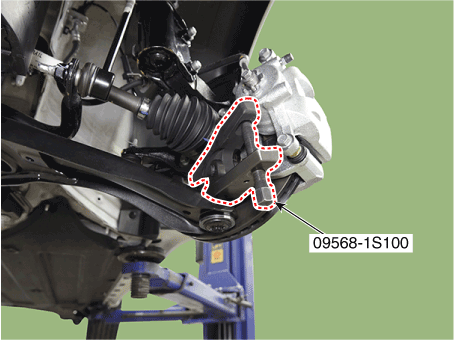
•
| Do not reuse the lower arm ball joint nut (A). |
|
|
6. | Separate the universal joint from the steering gear box after loosening the universal joint mounting bolt (A). Tightening torque : 49.0 - 58.8 N.m (5.0 - 6.0 kgf.m, 36.2 - 43.4 lb-ft) |
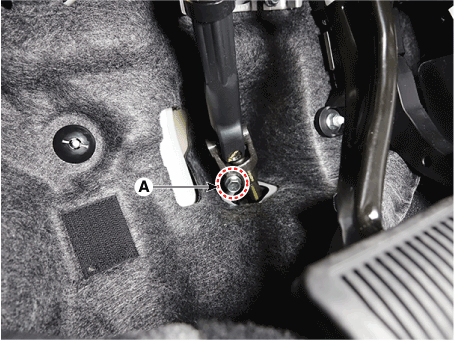
•
| Lock the steering wheel in the straight ahead position to prevent the damage of the clock spring inner cable. |
•
| When mounting, securely insert the universal joint into the steering gear box pinion shaft. |
•
| Do not reuse the universal joint bolt. |
•
| Assemble so that pinion shaft shark pin can be inserted between the joint slots. |
•
| Install by aligning the machining surface (A) of the universal joint and the machining surface (B) of the steering gearbox pinion shaft. 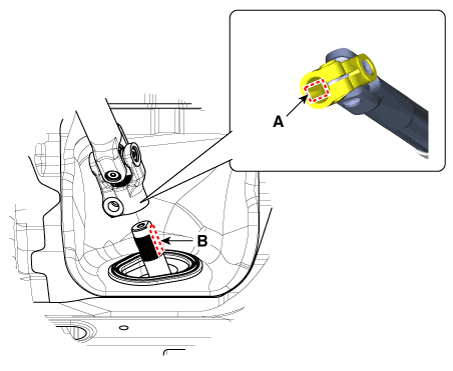
|
|
|
7. | Remove the engine room under cover. (Refer to Engine Mechanical System - "Engine Room Under Cover") |
8. | Remove the heat protector (A). Tightening torque 8.8 - 12.7 N.m (0.9 - 1.3 kgf.m, 6.5 - 9.4 lb-ft) |
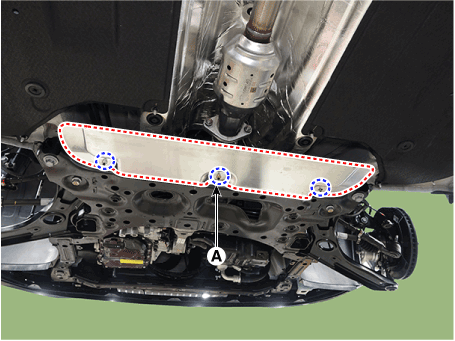
|
9. | Remove the muffler rubber hanger (A). 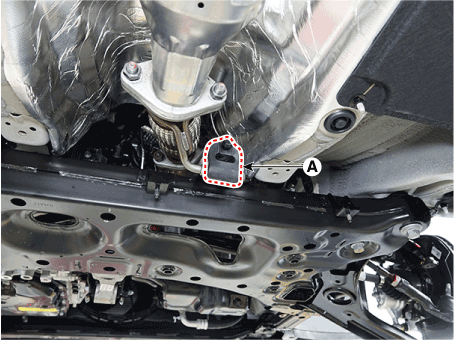
|
10. | Remove the roll rod bracket (C) after loosening the mounting bolts (A, B). Tightening torque (A) : 107.9 - 127.5 N.m (11.0 - 13.0 kgf.m, 79.6 - 94.0 lb-ft) (B) : 49.0 - 63.7 N.m (5.0 - 6.5 kgf.m, 36.2 - 47.0 lb-ft) |
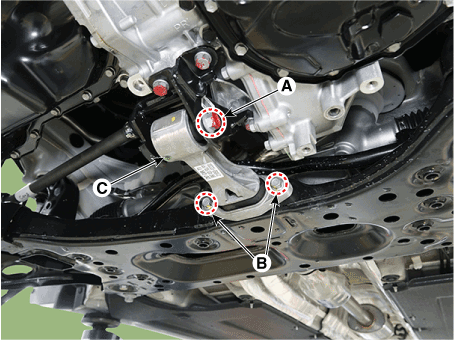
|
11. | Remove the fastener (A). [LH] 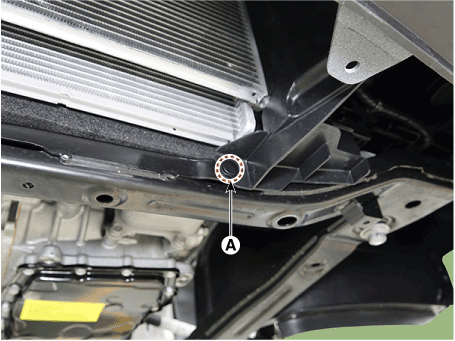
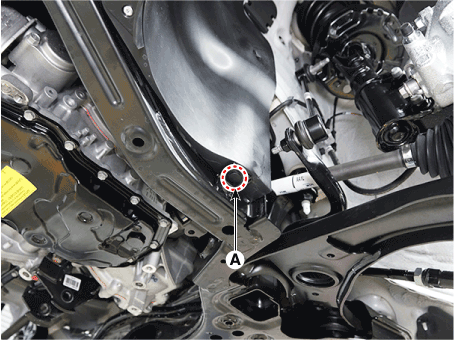
[RH] 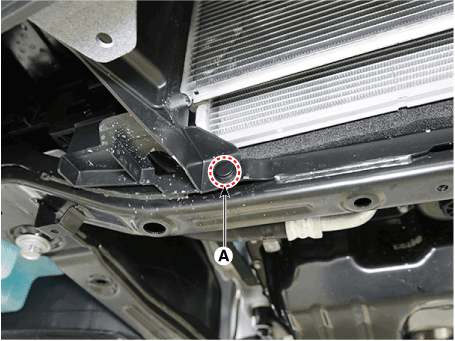
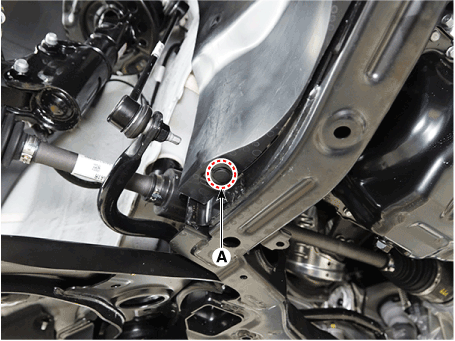
|
12. | Remove the sub frame after loosening the mounting bolts and nuts. Tightening torque : 176.5 - 196.1 N.m (18.0 - 20.0 kgf.m, 130.2 - 144.7 b-ft) |
•
| Set a transmission jack for safety. |
|
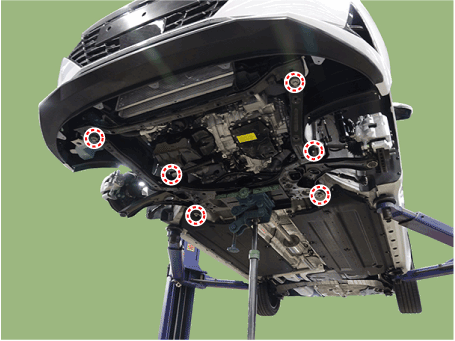
|
13. | Remove the heat protector (A). Tightening torque : 6.9 - 10.8 N.m (0.7 - 1.1 kgf.m, 5.1 - 8.0 lb-ft) |
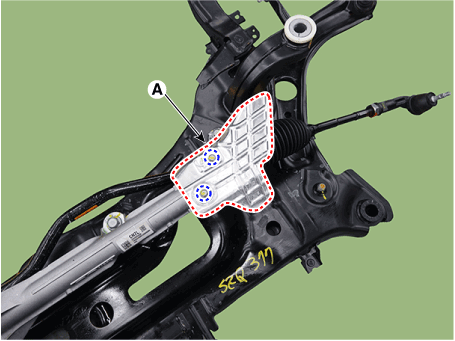

|
14. | Remove the steering gear box (A) from the sub frame after loosening the mounting bolts. Tightening torque : 107.9 - 127.5 N.m (11.0 - 13.0 kgf.m, 79.6 - 94.0 lb-ft) |
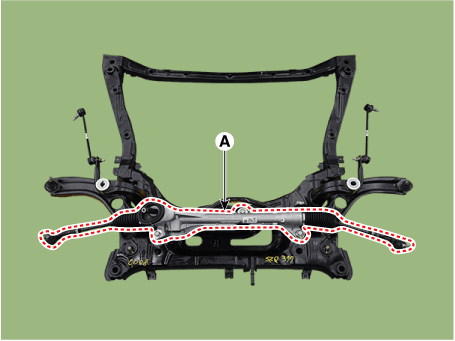
|
•
| Do not disassembly the steering gear box. |
•
| If disassembly the steering gear box, the quality(Noise / cleanliness / functions) is not guaranteed. 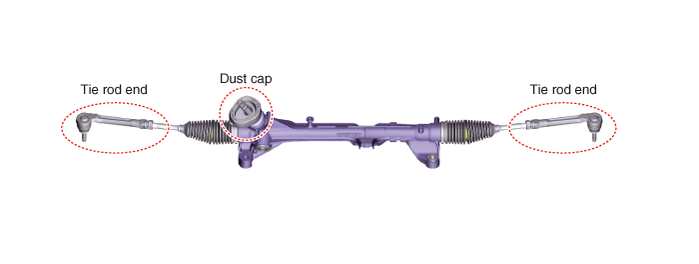
|
|
Tie rod end
1. | Remove the tie rod end after loosening the nut. Tightening torque : 49.0 - 53.9 N.m (5.0 - 5.5 kgf.m, 36.2 - 39.8 lb-ft) |
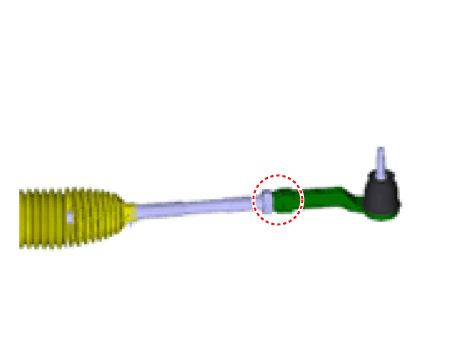
•
| Before removing the tie rod end, note by measuring the length of the thread or marked with paint. |
|
|
2. | Replace with new parts. |
3. | Check the front alignment. (Refer to Tires / Wheels - "Alignment") |
1. | To install, reverse the removal procedures. |
2. | Check the alignment. (Refer to Suspension System - "Alignment") |
MDPS Wiring
Repair procedures
•
| For DTC C125901 / C125929 / C125938 / C129002, refer to "CN7 MDPS DTC Diagnostic Guide". |
|
1. | Turn the ignition switch OFF and disconnect the battery negative (-) cable. •
| Disconnect the battery negative cable from the battery and then wait for at least 3 minutes. |
|
|
2. | Remove the fuse cover (A). 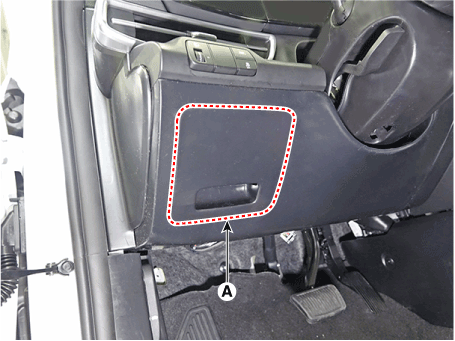
|
3. | Disconnect the grommet (A) and MDPS connector (B). 
•
| When removing the connector, separate it as follows. 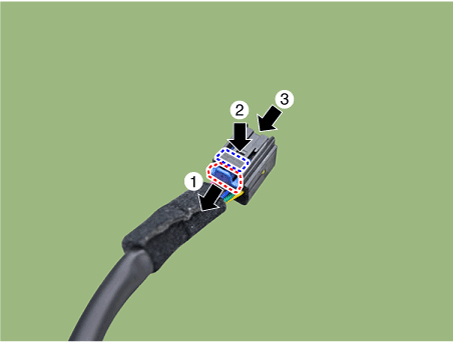
|
|
|
4. | Remove the wiring after disconnecting the MDPS connector (A). 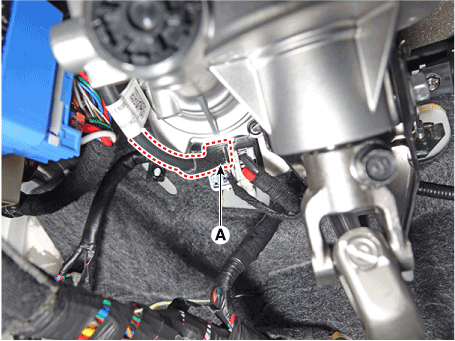
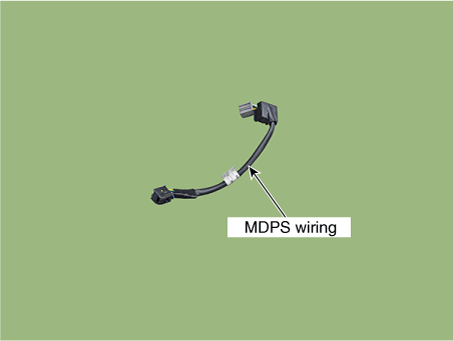
|
1. | To install, reverse the removal procedures. |
Components and components location
Components[G 1.6 MPI / LPI]1. Drive air bag module (DAB)2. Wiring3. Steering wheel4. Damper5. Remote control switch6. Switch bezel7. Lower cover[G 1.6 T-GDI]1. Lo ...