Disassembly
1. |
M/T : remove flywheel.
|
2. |
A/T : remove drive plate.
|
3. |
Install engine to engine stand for disassembly.
|
6. |
Remove oil level gauge assembly (A).
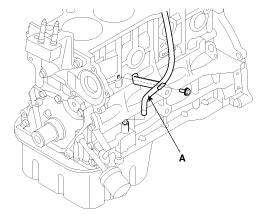
|
8. |
Remove oil pressure sensor (A).
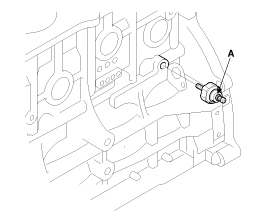
|
11. |
Remove oil screen.
Remove the 2bolts(C), oil screen (A) and gasket (B).
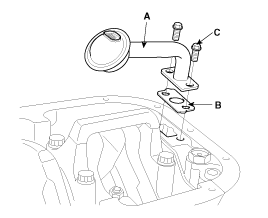
|
12. |
Check the connecting rod end play.
|
13. |
Remove the connecting rod caps and check oil clearance.
|
14. |
Remove piston and connecting rod assemblies.
(1) |
Using a ridge reamer, remove all the carbon from the top
of the cylinder.
|
(2) |
Push the piston, connecting rod assembly and upper bearing
through the top of the cylinder block.
• |
Keep the bearings, connecting rod and
cap together.
|
• |
Arrange the piston and connecting rod
assemblies in the correct order.
|
|
|
|
16. |
Remove rear oil seal case.
Remove the 5 bolts(B) and rear oil seal case (A).
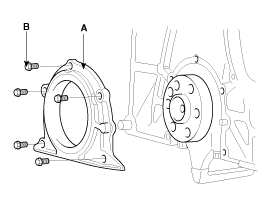
|
17. |
Remove crankshaft bearing cap and check oil clearance.
|
18. |
Check the crankshaft end play.
|
19. |
Lift the crankshaft (A) out of the engine, being careful not to
damage journals.
Arrange the main bearings and trust washers in the correct
order.
|
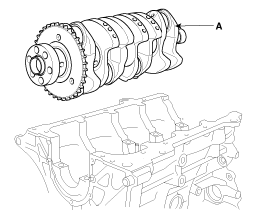
|
20. |
Check fit between piston and piston pin.
Try to move the piston back and forth on the piston pin. If any
movement is felt, replace the piston and pin as a set.
|
21. |
Remove piston rings.
(1) |
Using a piston ring expender, remove the 2 compression
rings.
|
(2) |
Remove the 2side rails and oil ring by hand.
Arrange the piston rings in the correct order
only.
|
|
|
22. |
Disconnect connecting rod from piston.
|
Inspection
Connecting Rod And Crankshaft
1. |
Check the connecting rod end play.
Using a feeler gauge, measure the end play while moving the connecting
rod back and forth.
Standard end play :
0.1~ 0.25mm(0.004 ~ 0.010in)
Maximum end play :
0.4mm(0.016in)
|
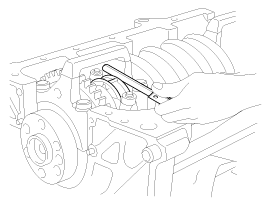
A. |
If out-of-tolerance, install a new connecting rod.
|
B. |
If still out-of-tolerance, replace the crankshaft.
|
|
2. |
Check the connecting road bearing oil clearance.
(1) |
Check the matchmarks on the connecting rod and cap are
aligned to ensure correct reassembly.
|
(2) |
Remove the 2 connecting rod cap nuts.
|
(3) |
Remove the connecting rod cap and bearing half.
|
(4) |
Clean the crank pin and bearing.
|
(5) |
Place plastigage across the crank pin.
|
(6) |
Reinstall the bearing half and cap, and torque the nuts.
Tightening torque
49.0 ~ 52.0 Nm (5.0 ~ 5.3kgf.m, 36.2 ~ 38.3lb-ft)
|
Do not turn the crankshaft.
Always use a new connecting rod cap nuts.
|
|
(7) |
Remove the 2 nuts, connecting rod cap and bearing half.
|
(8) |
Measure the plastigage at its widest point.
Standard oil clearance
0.024 ~ 0.042mm(0.0009 ~ 0.0017in)
|
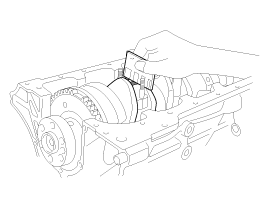
|
(9) |
If the plastigage measures too wide or too narrow, remove
the upper half of the bearing, install a new, complete bearing
with the same color mark (select the color as shown in the next
column), and recheck the clearance.
Do not file, shim, or scrape the bearings or the
caps to adjust clearance.
|
|
(10) |
If the plastigage shows the clearance is still incorrect,
try the next larger or smaller bearing (the color listed above
or below that one), and check clearance again.
If the proper clearance cannot be obtained by
using the appropriate larger or smaller bearings, replace
the crankshaft and start over.
|
If the marks are indecipherable because of an
accumulation of dirt and dust, do not scrub them with
a wire brush or scraper. Clean them only with solvent
or detergent.
|
Connecting Rod Mark Location
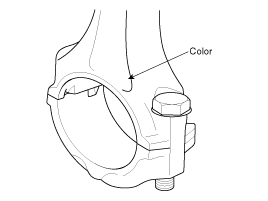
Discrimination Of Connecting Rod
Class
|
Mark
|
Inside Diameter
|
A
|
White
|
48.00 ~ 48.006mm
(1.8896 ~ 1.8899in.)
|
B
|
None
|
48.006 ~ 48.012mm
(1.8899 ~ 1.8902in.)
|
C
|
Yellow
|
48.012 ~ 48.018mm
(1.8902 ~ 1.8904in.)
|
Crankshaft Pin Mark Location
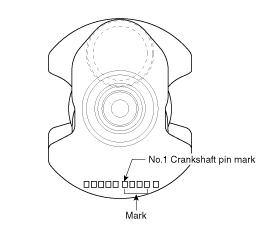
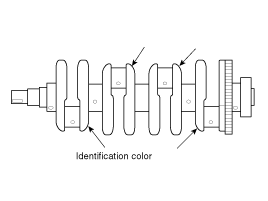
Discrimination Of Crankshaft
Class
|
Mark
|
Outside Diameter Of Pin
|
I
|
Yellow
|
44.960 ~ 44.966mm
(1.7700 ~ 1.7703in.)
|
II
|
None
|
44.954 ~ 44.960mm
(1.7698 ~ 1.7700in.)
|
III
|
White
|
44.948 ~ 44.954mm
(1.7696 ~ 1.7698in.)
|
Place Of Identification Mark (Connecting Rod Bearing)
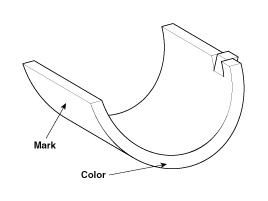
Discrimination Of Connecting Rod Bearing
Class
|
Mark
|
Thickness Of Bearing
|
AA
|
Blue
|
1.514 ~ 1.517mm
(0.0596 ~ 0.0597in.)
|
A
|
Black
|
1.511 ~ 1.514mm
(0.0595 ~ 0.0596in.)
|
B
|
None
|
1.508 ~ 1.511mm
(0.0594 ~ 0.0595in.)
|
C
|
Green
|
1.505 ~ 1.508mm
(0.0593 ~ 0.0594in.)
|
D
|
Yellow
|
1.502 ~ 1.505mm
(0.0591 ~ 0.0593in)
|
|
(11) |
Selection
Crankshaft Indentification
Mark
|
Connecting Rod Identification
Mark
|
Assembing Classification
Of Bearing
|
I (Yellow)
|
A (White)
|
D (Yellow)
|
B (None)
|
C (Green)
|
C (Yellow)
|
B (None)
|
II (None)
|
A (White)
|
C (Green)
|
B (None)
|
B (None)
|
C (Yellow)
|
A (Black)
|
III (White)
|
A (White)
|
B (None)
|
B (None)
|
A (Black)
|
C (Yellow)
|
AA (Blue)
|
|
|
3. |
Check the crankshaft bearing oil clearance.
(1) |
To check main bearing-to-journal oil clearance, remove
the main caps and bearing halves.
|
(2) |
Clean each main journal and bearing half with a clean
shop tower.
|
(3) |
Place one strip of plastigage across each main journal.
|
(4) |
Reinstall the bearings and caps, then torque the bolts.
Tightening torque :
27.5~31.4Nm (2.8~3.2kgf.m, 20.3~23.11lb-ft) +
60° ~ 64°
|
Do not turn the crankshaft.
Always use a new main bearing cap bolts.
|
|
(5) |
Remove the cap and bearing again, and measure the widest
part of the plastigage.
Standard oil clearance
:
0.028 ~ 0.046mm (0.0011 ~ 0.0018in)
|
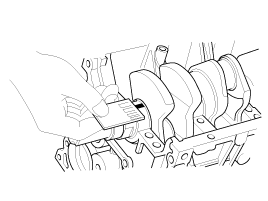
|
(6) |
If the plastigage measures too wide or too narrow, remove
the upper half of the bearing, install a new, complete bearing
with the same color mark (select the color as shown in the next
column), and recheck the clearance.
Do not file, shim, or scrape the bearings or the
caps to adjust clearance.
|
|
(7) |
If the plastigage shows the clearance is still incorrect,
try the next larger or smaller bearing (the color listed above
or below that one), and check clearance again.
If the proper clearance cannot be obtained by
using the appropriate larger or smaller bearings, replace
the crankshaft and start over.
|
If the marks are indecipherable because of an
accumulation of dirt and dust, do not scrub them with
a wire brush or scraper. Clean them only with solvent
or detergent.
|
|
|
Connecting rods
1. |
When reinstalling, make sure that cylinder numbers put on the
connecting rod and cap at disassembly match. When a new connecting rod
is installed, make sure that the notches for holding the bearing in
place are on the same side.
|
2. |
Replace the connecting rod if it is damaged on the thrust faces
at either end. Also if step wear or a severely rough surface of the
inside diameter of the small end is apparent, the rod must be replaced
as well.
|
3. |
Using a connecting rod aligning tool, check the rod for bend and
twist. If the measured value is close to the repair limit, correct the
rod by a press. Any connecting rod that has been severely bent or distorted
should be replaced.
Allowable bend of connecting
rod :
0.05mm / 100mm (0.0020 in./3.94 in) or less
Allowable twist of connecting
rod :
0.1mm / 100mm (0.0039 in./3.94 in) or less
|
Letters have been stamped on the end of the block as a mark for
the size of each of the 5 main journal bores.
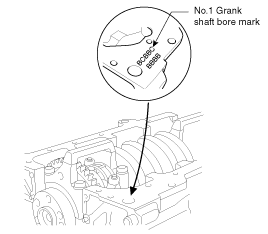
Discrimination Of Cylinder Block
Calss
|
Mark
|
Inside Diameter
|
a
|
A
|
59.000 ~ 59.006mm
(2.3228 ~ 2.3230in.)
|
b
|
B
|
59.006 ~ 59.012mm
(2.3230 ~ 2.3233in.)
|
c
|
C
|
59.012 ~ 59.018mm
(2.3233 ~ 2.3235in.)
|
Crankshaft Journal Mark Location
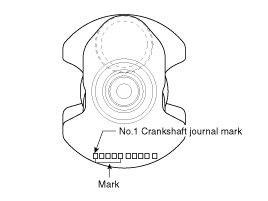
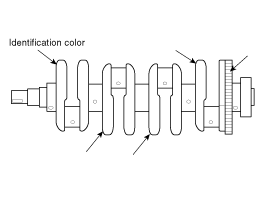
Discrimination Of Crankshaft
Class
|
Mark
|
Outside Diameter Of Journal
|
I
|
Yellow
|
54.956 ~ 54.962mm
(2.1636 ~ 2.1638in.)
|
II
|
None
|
54.950 ~ 54.956mm
(2.1633 ~ 2.1636in.)
|
III
|
White
|
54.944 ~ 54.950mm
(2.1631 ~ 2.1633in.)
|
Place Of Identification Mark (Crankshaft Bearing)
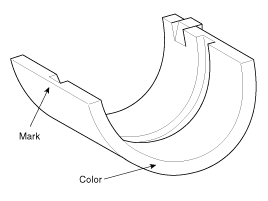
Discrimination Of Crankshaft Bearing
Class
|
Mark
|
Thickness Of Bearing
|
AA
|
Blue
|
2.014 ~ 2.017mm
(0.0793 ~ 0.0794in.)
|
A
|
Black
|
2.011 ~ 2.014mm
(0.0791 ~ 0.0793in.)
|
B
|
None
|
2.008 ~ 2.011mm
(0.0790 ~ 0.0791in.)
|
C
|
Green
|
2.005 ~ 2.008mm
(0.0789 ~ 0.790in.)
|
D
|
Yellow
|
2.002 ~ 2.005mm
(0.0788 ~ 0.0789in.)
|
Selection
Crankshaft Identification Mark
|
Crankshaft Bore Identification Mark
|
Assembling Classification Of Bearing
|
I (Yellow)
|
a (A)
|
D (Yellow)
|
b (B)
|
C (Green)
|
c (C)
|
B (None)
|
II (None)
|
a (A)
|
C (Green)
|
b (B)
|
B (None)
|
c (C)
|
A (Black)
|
III (White)
|
a (A)
|
B (None)
|
b (B)
|
A (Black)
|
c (C)
|
AA (Blue)
|
|
4. |
Check crankshaft end play.
Using a dial indicator, measure the thrust clearance while prying
the crankshaft back and forth with a screwdriver.
Standard end play :
0.06 ~ 0.26mm (0.0023 ~ 0.010in)
Limit : 0.30mm
(0.0118in)
|
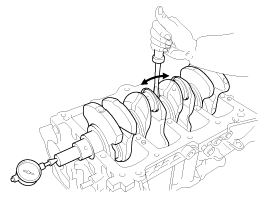
If the end play is greater than maximum, replace the thrust bearings
as a set.
Thrust bearing thickness :
2.44 ~ 2.47mm(0.096 ~ 0.097in)
|
|
5. |
Inspect main journals and crank pins
Using a micrometer, measure the diameter of each main journal
and crank pin.
Main journal diameter :
56.942 ~ 56.962mm (2.2418~2.2426in)
Crank pin diameter :
44.946 ~ 44.966mm (1.7695 ~ 1.7703in)
|
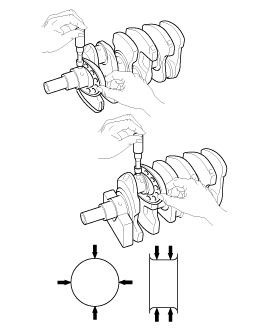
|
Cylinder Block
1. |
Remove gasket material.
Using a gasket scraper, remove all the gasket material from the
top surface of the cylinder block.
|
2. |
Clean cylinder block
Using a soft brush and solvent, thoroughly clean the cylinder
block.
|
3. |
Inspect top surface of cylinder block for flatness.
Using a precision straight edge and feeler gauge, measure the
surface contacting the cylinder head gasket for warpage.
Flatness of cylinder block gasket
surface
Standard : Less than 0.03mm(0.0012 in)
Limit : 0.05 mm (0.0020 in)
|
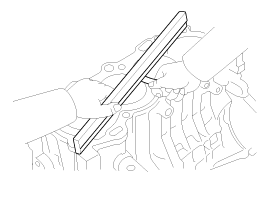
|
4. |
Inspect cylinder bore diameter
Visually check the cylinder for vertical scratchs.
If deep scratches are present, replace the cylinder block.
|
5. |
Components
1. Oil screen
2. Gasket
3. Crankshaft
4. Oil seal
5. Front case
6. Thrust bearing
7. Drive plate
8. Washer
9. Adapter plate
10 ...
|