Air Cleaner
Components and components location
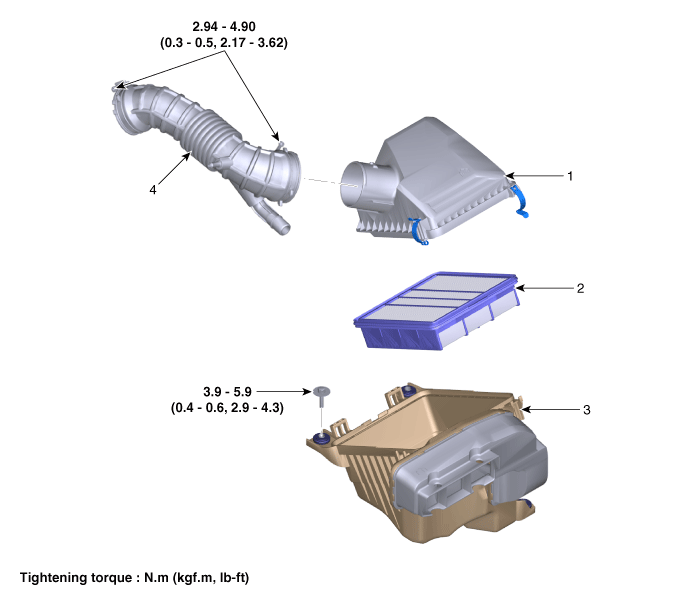
1. Air cleaner cover 2. Air cleaner element
| 3. Air cleaner body & air duct 5. Air intake hose
|
Repair procedures
Air Cleaner Assembly.
1. | Disconnect the battery negative terminal. |
2. | Disconnect the breather hose (A). 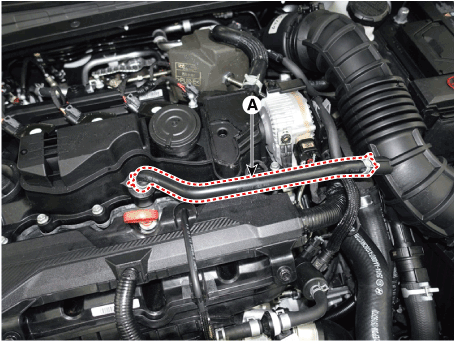
|
3. | Disconnect the RCV hose (A). 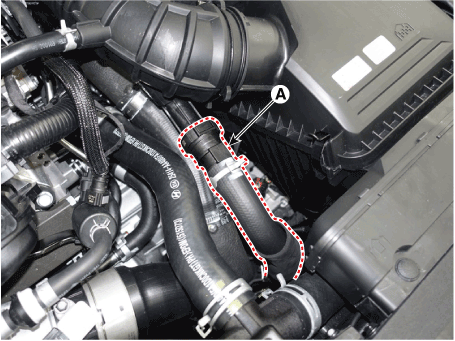
|
4. | Disconnect the air intake hose (A), and then remove the air cleaner assembly (B). Tightening torque : Intake hose clamp : 2.9 - 4.9 N.m (0.3 - 0.5 kgf.m, 2.2 - 3.6 lb-ft) Air cleaner assembly : 3.9 - 5.9 N.m (0.4 - 0.6 kgf.m, 2.9 - 4.3 Ib-ft) |
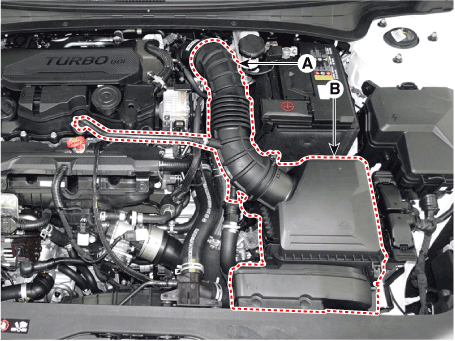
•
| When assembling the intake hose, match the alignment marks (A). |

|
|
5. | Install in the reverse order of removal. |
Air Cleaner Element Replacement
1. | Open the air cleaner cover by unhooking the clamps (A). 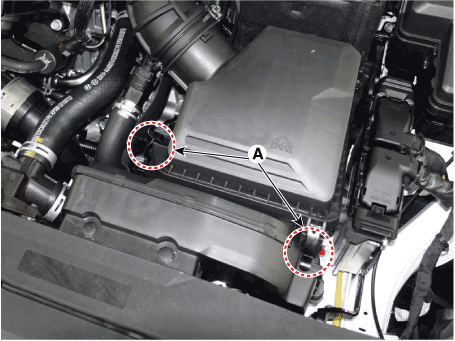
|
2. | Replace the air cleaner element (A) with a new one. 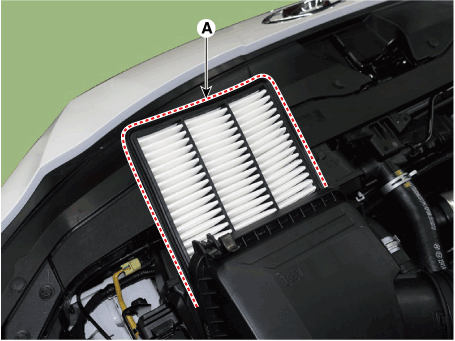
•
| If there are foreign substances inside the air cleaner assembly, wipe the inside of the air cleaner assembly and then replace the air cleaner element. |
|
|
3. | Close the air cleaner cover by hooking the clamps. 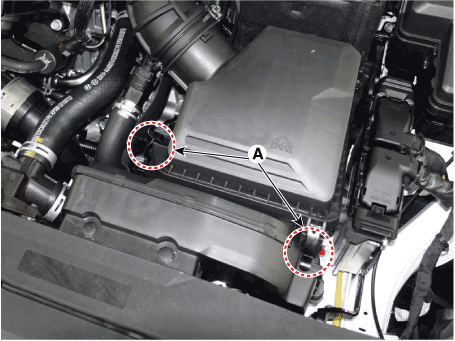
•
| Install the air cleaner cover, insert the hinge (A) and fill the clamp. 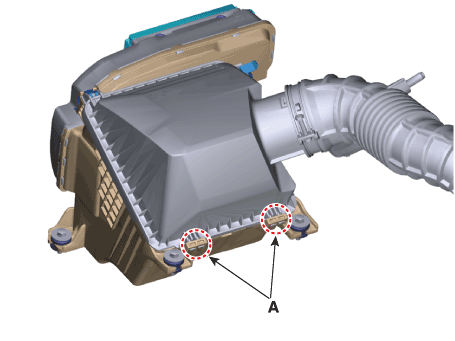
|
|
|
Intake Manifold
Components and components location
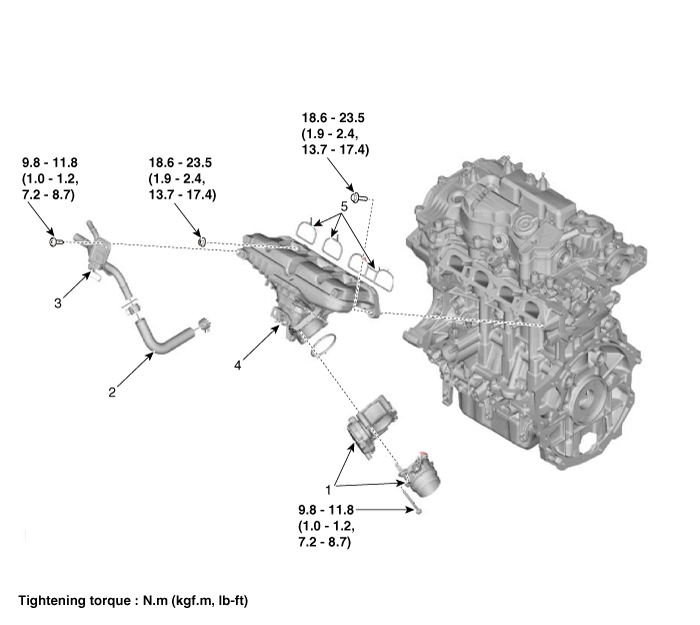
1. Electronic throttle body (ETC) 2. Return hose 3. Return pipe
| 4. Intake manifold 5. Intake manifold gasket
|
Repair procedures
1. | Disconnect the battery negative terminal. |
2. | Remove the engine cover. (Refer to Engine and Transaxle Assembly - "Engine Cover") |
3. | Remove the engine wire harness connectors and wire harness clamps from cylinder head and the intake manifold. 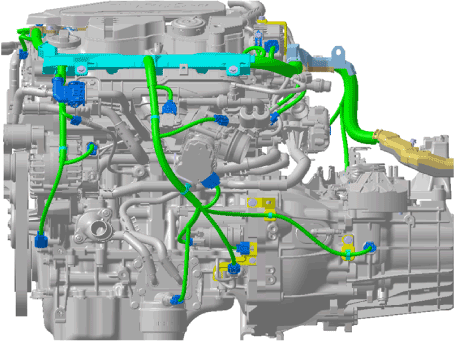
|
4. | Disconnect the intercooler outlet hose (A). 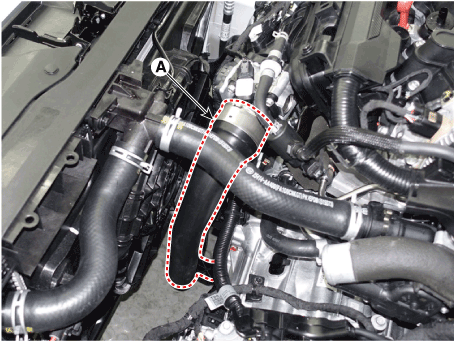
1) | When disconnecting the intercooler hose, pull the quick connector clamp (A) in the direction of the arrow as below. 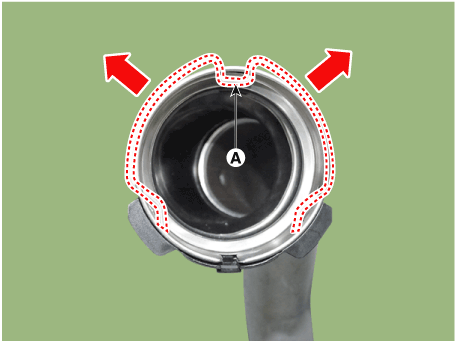
|
2) | Move the quick connector clamp from B to C position as below and then disconnect by pulling the quick connector hose. 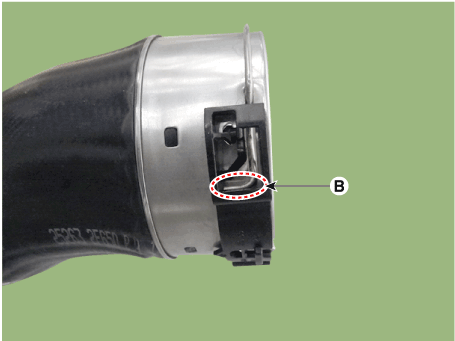
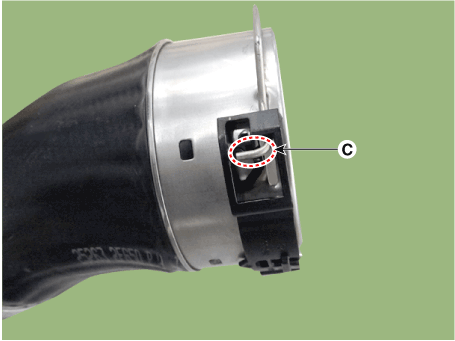
|
|
|
5. | Remove the purge control solenoid valve (PCSV) hose (A). 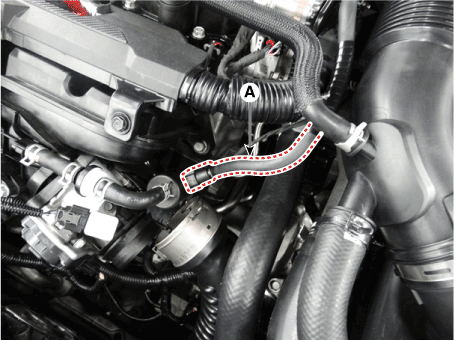
|
6. | Remove the water return hose & pipe bracket bolts (A). Tightening torque : 9.8 - 11.8 N.m (1.0 - 1.2 kgf.m, 7.2 - 8.7 lb-ft) |
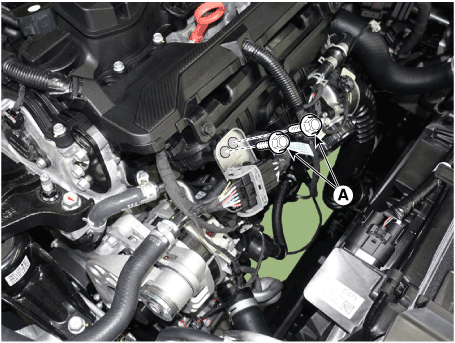
|
7. | Remove the Intake Manifold (A). Tightening torque : 18.6 - 23.5 N.m (1.9 - 2.4 kgf.m, 13.7 - 17.4 lb-ft) |
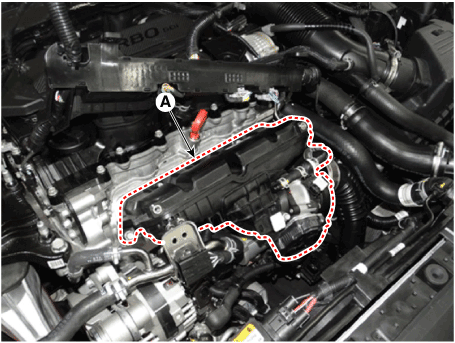
•
| When installing, replace with new gaskets. When installing the intake manifold, tighten sequence shown. 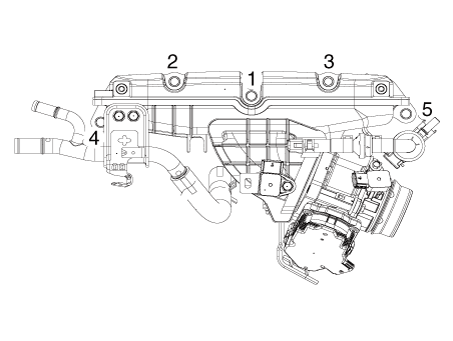
|
|
|
8. | Install in the reverse order of removal. |
Exhaust Manifold
Components and components location
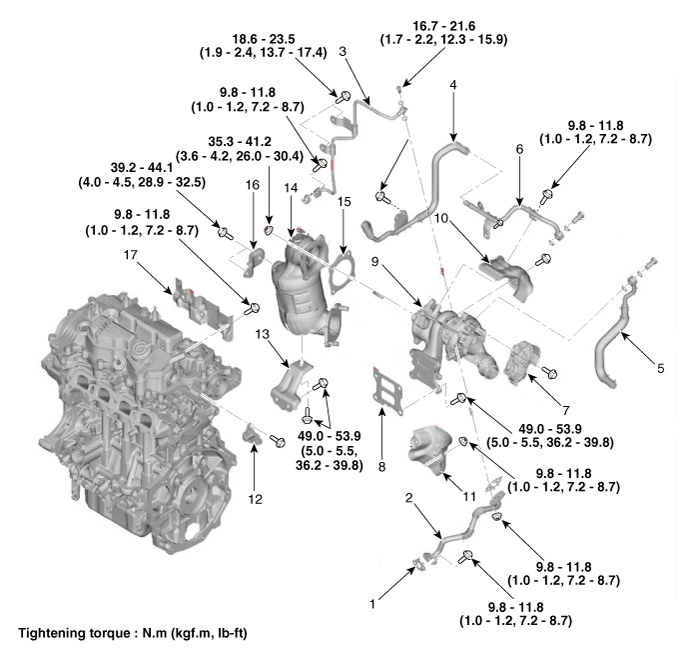
1. Oil drain pipe gasket 2. Oil drain pipe 3. Oil feed pipe 4. Torbo charhe water outlet hose & pipe B 5. Torbo charhe water inlet pipe 6. Torbo charhe water outlet pipe A 7. Electric waste gate actuator (EWGA) 8. Exhaust manifold gasket 9. Exhaust manifold & Turbo charger
| 10. Exhaust manifold heat protector A 11. Exhaust manifold heat protector B 12. Intercooler pipe braket 13. Exhaust manifold & Turbo charger stay bracket 14. Warm up catalytic converter 15. Warm up catalytic converter gasket 16. Warm up catalytic converter upper stay bracket 17. Cylinder head heat peotector
|
Repair procedures
1. | Disconnect the negative battery terminal. |
2. | Remove the engine cover. (Refer to Engine and Transaxle Assembly - "Engine Cover") |
3. | Remove the engine room under cover. (Refer to Engine and Transaxle Assembly - "Engine Room Under Cover") |
4. | Drain the coolant. (Refer to Cooling System - "Coolant") |
5. | Disconnect the engine ground cable (A). Tightening torque : 10.8 - 13.7 N.m (1.1 - 1.4 kgf.m, 8.0 - 10.1 lb-ft) |

|
6. | Install the jack to the edge of oil pan. 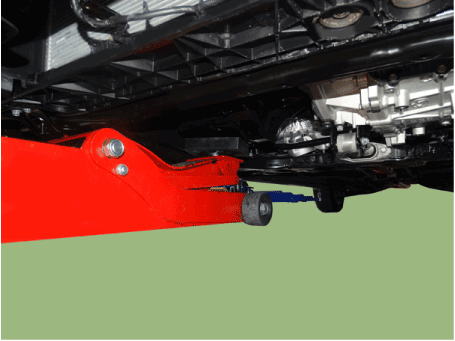
•
| Insert the rubber block between jack and oil pan. |
|
|
7. | Remove the engine mounting support bracket (A). Tightening torque : Nut (B) : 88.3 - 107.9 N.m (9.0 - 11.0 kgf.m, 65.1 - 79.6 lb-ft) Bolt, Nuts (C) : 58.8 - 73.6 N.m (6.0 - 7.5 kgf.m, 43.4 - 54.2 lb-ft) |
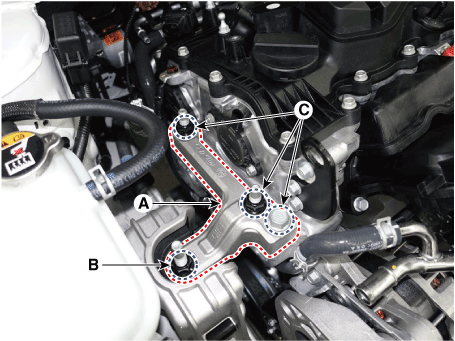
|
8. | Disconnect the turbo charger outlet hose (A). 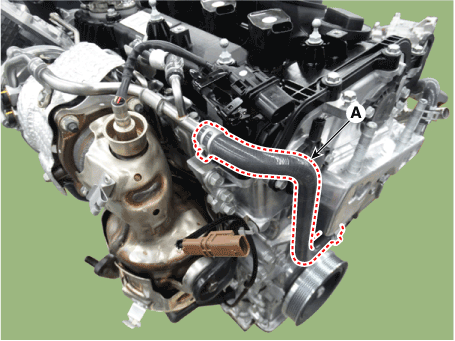
|
9. | Remove the warm up catalytic converter(WCC) upper stay bracket (A). Tightening torque : 39.2 - 44.1 N.m (4.0 - 4.5 kgf.m, 28.9 - 32.5 lb-ft) |
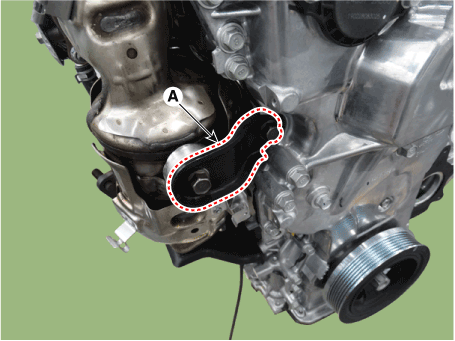
•
| When installing, temporarily tighten the nut in picture order. 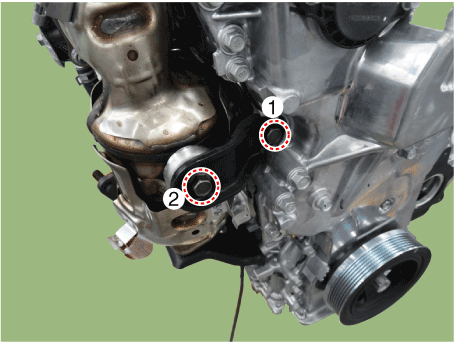
|
|
|
10. | Remove the front muffler. (Refer to Intake and Exhaust Manifold - "Front Muffler") |
11. | Remove the warm up catalytic converter(WCC) lower stay bracket (A). Tightening torque : 49.1 - 54.0 N.m (5.0 - 5.5 kgf.m, 36.2 - 39.8 lb-ft) |
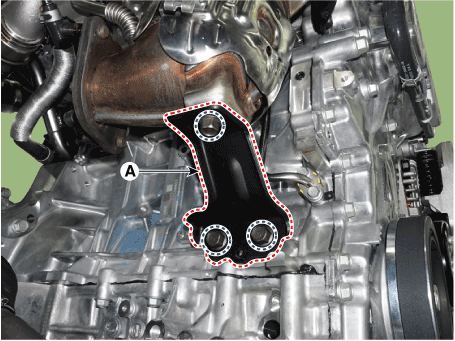
•
| When installing, temporarily tighten the nut in picture order. 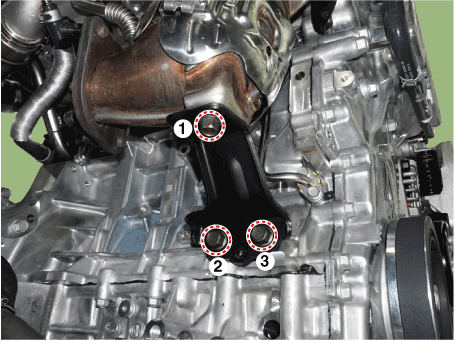
|
|
|
12. | Remove the warm up catalytic converter (WCC) (A). Tightening torque : 35.3 - 41.2 N.m (3.6 - 4.2 kgf.m, 26.0 - 30.4 lb-ft) |
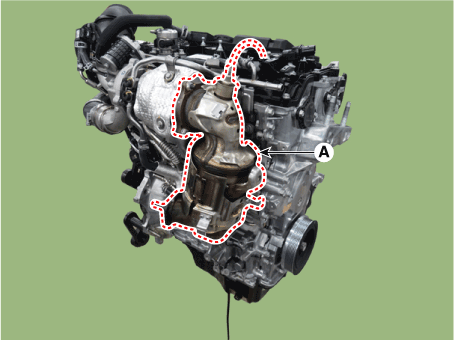
•
| When installing, replace with a new gasket. |
|
|
13. | Remove the air duct and air cleaner assembly. (Refer to Intake and Exhaust System - "Air Cleaner") |
14. | Remove the battery and battery tray. (Refer to Engine Electrical System - "Battery") |
15. | Disconnect the turbo charger intake hoseB (A). 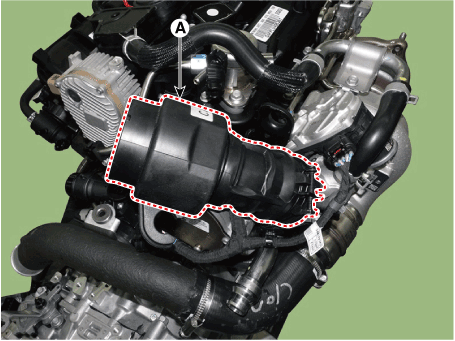
|
16. | Remove the tbreather hose and pipe (A). 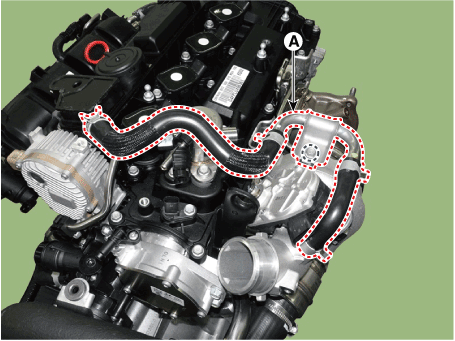
|
17. | Remove the turbo charger inlet pipe (A). 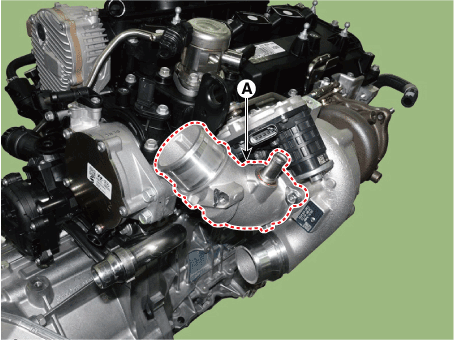
|
18. | Disconnect the intercooler inlet hose (A). Tightening torque : Clamp bolt : 4.9 - 6.9 N.m (0.5 - 0.7 kgf.m, 3.6 - 5.1 lb-ft) |
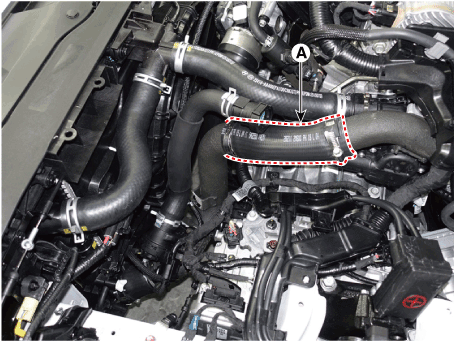
•
| Insert the hose until it reaches the end of stopper. |
•
| When installing the intercooler inlet hose, Match the alignment marks. |
|
|
19. | Remove the intercooler hose & pipe (A). Tightening torque : Mounting bolt : 18.6 - 23.5 N.m (1.9 - 2.4 kgf.m, 13.7 - 17.4 lb-ft) Clamp bolt : 4.9 - 6.9 N.m (0.5 - 0.7 kgf.m, 3.6 - 5.1 lb-ft) |
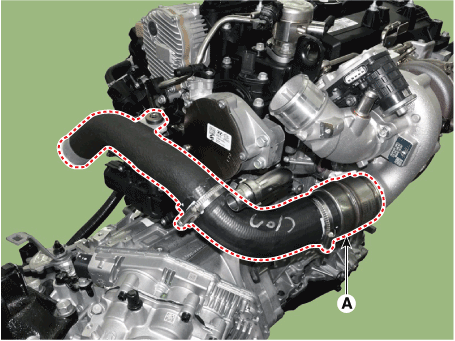
•
| Insert the hose until it reaches the end of stopper. |
•
| When installing the intercooler inlet hose, Match the alignment marks. |
|
|
20. | Disconnect the turbo charger outlet hose (A), and then remove the water pipe (B). Tightening torque : Bracket bolts : 9.8 - 11.8 N.m (1.0 - 1.2 kgf.m, 7.2 - 8.7 lb-ft) Eye bolt : 34.3 - 39.2 N.m (3.5 - 4.0 kgf.m, 25.3 - 28.9 lb-ft) |
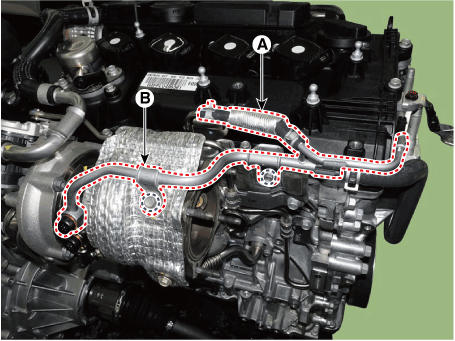
•
| When installing, replace with a new eye bolt gasket. |
•
| When installing, provisionally tighten the bracket bolts and eyebolt and then tighten the eyebolt with specified torque. |
|
|
21. | Remove the turbo charger inlet hose & pipe (A). Tightening torque : Eye bolt : 34.3 - 39.2 N.m (3.5 - 4.0 kgf.m, 25.3 - 28.9 lb-ft) |
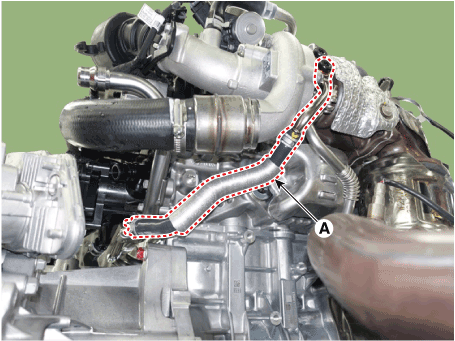
•
| When installing, replace with a new eye bolt gasket. |
|
|
22. | Remove the turbo charger heat protect (A). Tightening torque : 9.8 - 11.8 N.m (1.0 - 1.2 kgf.m, 7.2 - 8.7 lb-ft) |
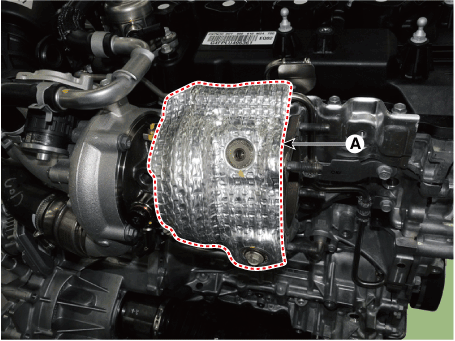
|
23. | Remove the turbo charger oil drain pipe(A). Tightening torque : 9.8 - 11.8 N.m (1.0 - 1.2 kgf.m, 7.2 - 8.7 lb-ft) |
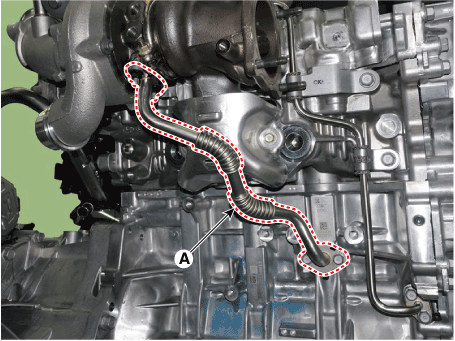
•
| When installing, replace with a new gasket. |
|
|
24. | Remove the turbo charger oil feed pipe(A). Tightening torque : Oil feed eye bolt : 16.7 - 21.6 N.m (1.7 - 2.2 kgf.m, 12.3 - 15.9 lb-ft) Oil feed pipe : 9.8 - 11.8 N.m (1.0 - 1.2 kgf.m, 7.2 - 8.7 lb-ft) Oil feed pipe bracket bolt : 18.6 - 23.5 N.m (1.9 - 2.4 kgf.m, 13.7 - 17.4 lb-ft) |
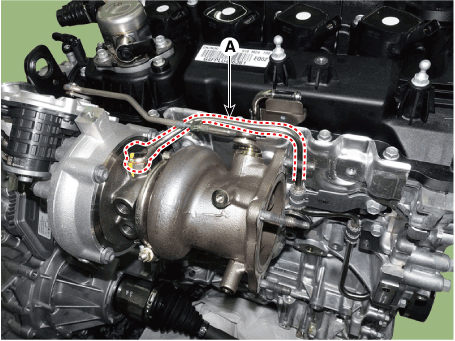
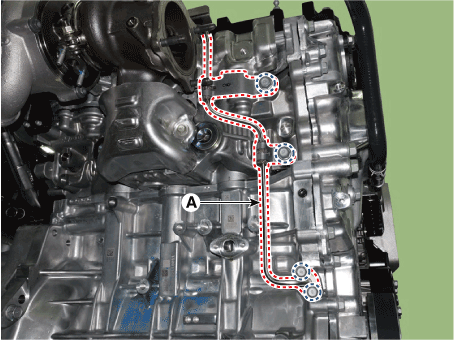
•
| When installing, replace with a new gasket. |
|
|
25. | Remove the turbo charger heat protector (A). Tightening torque : 9.8 - 11.8 N.m (1.0 - 1.2 kgf.m, 7.2 - 8.7 lb-ft) |
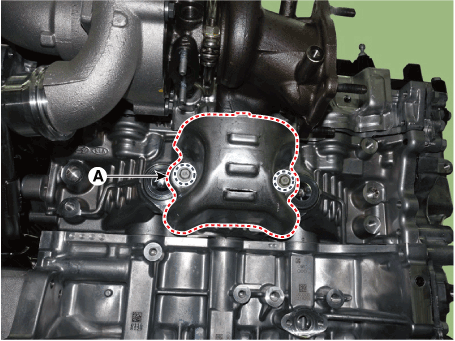
|
26. | Remove the exhaust manifold & turbo charger (A). Tightening torque : 49.1 - 54.0 N.m (5.0 - 5.5 kgf.m, 36.2 - 39.8 lb-ft) |
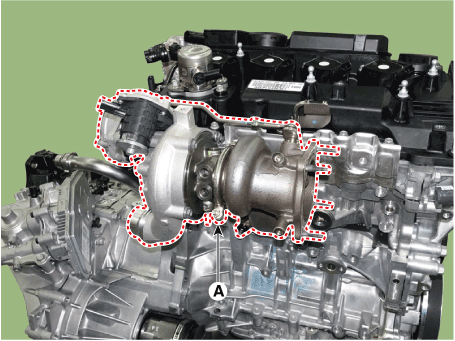
•
| When installing the exhaust manifold tighten the nuts with specified torque in the sequence shown. 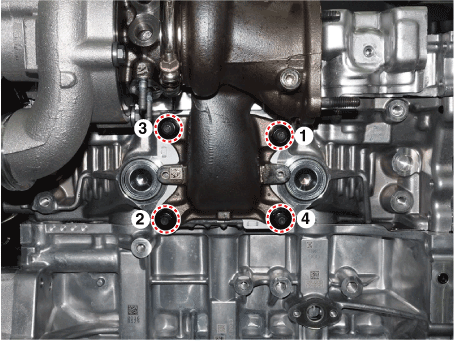
|
|
|
27. | Remove the exhaust manifold & turbo charger gasket (A). 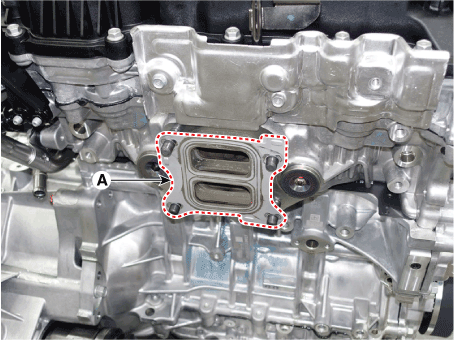
•
| When installing, replace with a new gasket. |
|
|
28. | Remove the C- ring, and then remove the electric WGT control actuator (A) after loosening the mounting bolts. 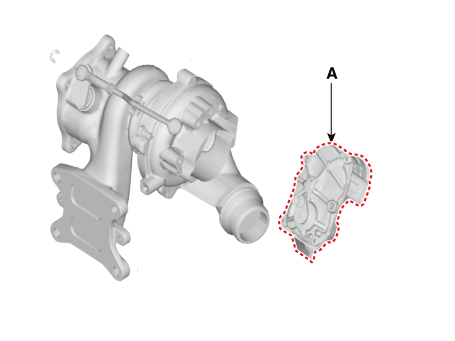
|
29. | Install in the reverse order of removal. •
| Adjust the EWGA. (Refer to Engine Control / Fuel System - "Electric WGT Control Actuator") |
|
|
Turbo Charger
Repair procedures
1. | Remove the Turbocharger & Exhaust Manifold. (Intake And Exhaust System - "Exhaust Manifold") |
Turbocharger Diagnostic Flow |
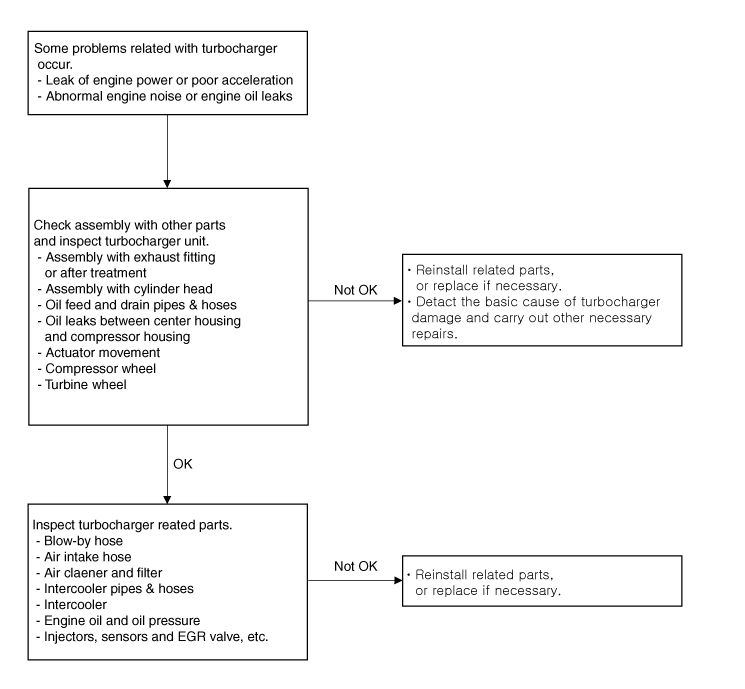
If any problem related with turbocharger, such as lack of engine power, poor acceleration, abnormal engine noise or oil leaks, may occur, check the turbocharger according to the procedure as follows.
1. | Check the assembly of the turbocharger and the exhaust fitting (or the after treatment). –
| Check that a gasket is installed. |
–
| Check that mounting bolts (or nuts) are tightened properly. |
–
| Check for any damage, such as crack, on the parts. |
Gas leakage caused by lack of gasket or inadequately tightened mounting bolts (or nuts) may cause abnormal engine noise. If the cause of the problem is detected, retighten the mounting bolts (or nuts) to the specified torque or replace the gasket or damaged parts with new ones if necessary. |
2. | Check the assembly of the exhaust manifold and the cylinder head. –
| Check that a gasket is installed. |
–
| Check that the mounting bolts (or nuts) are tightened properly. |
Gas leakage caused by lack of gasket or inadequately tightened mounting bolts (or nuts) may cause abnormal engine noise. If the cause of the problem is detected, retighten the mounting bolts (or nuts) to the specified torque or install a new gasket if necessary. |
3. | Check the turbocharger oil feed pipe & hose and oil drain pipe & hose. –
| Check that a gasket is installed. |
–
| Check if the mounting bolts are tightened properly. |
–
| Check if the clamps are positioned in place. |
–
| Check if the oil pipes & hoses are damaged (bent, crushed, torn or cracked). |
If a gas leak occur as a gasket was not installed or mounting bolts were tightened inadequately, it may cause oil leaks. If the oil feed pipe & hose is damaged, engine oil is not supplied sufficiently to the turbocharger then it may damage the turbocharger. If the oil drain pipe & hose is damaged and clogged, engine oil is not drained smoothly then it may cause oil leaks from the turbocharger. If the cause of the problem is detected, retighten the mounting bolts (or nuts) to the specified torque or replace the gasket or damaged parts with new ones if necessary. |
4. | Check for oil leakage between center housing and compressor housing. –
| Check that the mounting bolts are tightened properly. |
Damaged O-ring (gasket) between the center housing and the compressor housing may cause oil leakage. If an oil leak is detected, replace the turbocharger with a new one. |
5. | Inspect the rod unit of the electric waste gate actuator (EWGA). –
| Check that the rod setting marks (A) of the EWGA match. 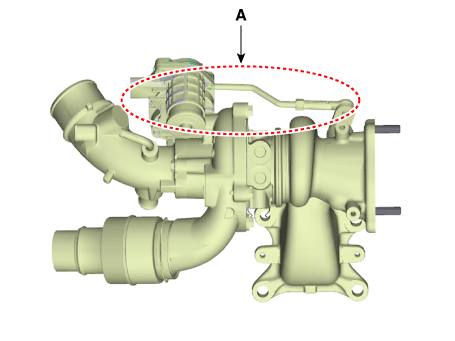
|
Damaged turbocharger actuator may cause lack of engine power and poor acceleration. If the actuator rod does not move, replace the turbocharger with a new one. |
6. | Check the electric waste gate actuator (EWGA). –
| Electric waste gate actuator (EWGA) : Check for movement of the actuator rod when a forced actuator operating mode is performed by diagnostic tool. (Refer to DTC guide) 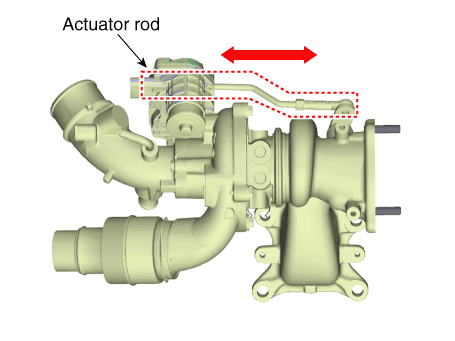
If the turbocharger actuator is damaged, it may cause lack of engine power and poor acceleration. If the actuator rod does not move, replace the turbocharger with a new one. |
|
7. | Check the turbocharger compressor wheel. –
| Check if the compressor wheel is damaged (bent or deformed). |
–
| Check that the compressor wheel rotates smoothly. e.g. 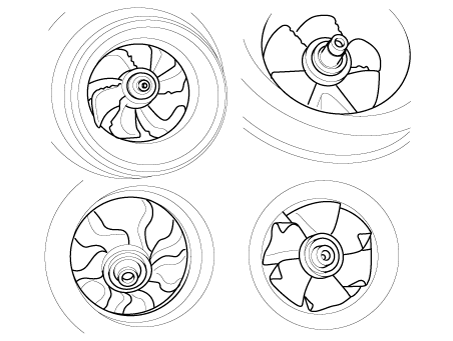
|
Damaged compressor wheel may cause abnormal noise from the turbocharger and poor acceleration. If the compressor wheel are damaged or deformed, replace the turbocharger with a new one. |
8. | Check the turbocharger turbine wheel. –
| Check if the turbine wheel is damaged. |
–
| Check that the turbine wheel rotates smoothly. e.g. 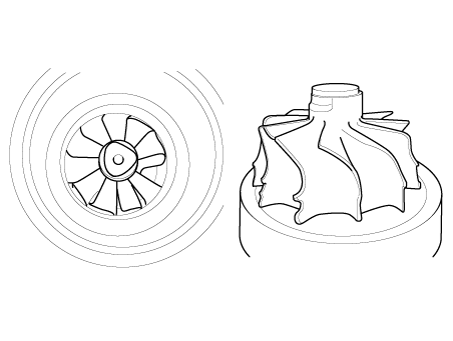
|
Damaged turbine wheel may cause abnormal noise from the turbocharger and poor acceleration. If the turbine wheel are damaged or deformed, replace the turbocharger with a new one. |
If no problem is detected from the turbocharger, check the turbocharger-related parts according to the procedure as follows.
9. | Check the blow-by hose. (Refer to FL group) –
| Check if the breather hose is damaged (bent, clogged). |
–
| Check if the positive crankcase ventilation (PCV) valve is clogged. |
If the breather hose is bent or clogged, the internal pressure in the engine will increase and engine oil will not be supplied smoothly to the turbocharger, causing damage to the turbocharger and oil leakage. If the cause of the problem is detected, replace the breather hose or the related parts with new ones. |
10. | Check the air intake hose connected to the turbocharger. –
| Check if the air intake hose is damaged (bent, crushed, detached or torn). |
If the cross-section of the hose diminishes as the air intake hose is bent or crushed, intake air to the turbocharger will be reduced and the pressure in front of turbocharger will drop, causing damage to the turbocharger or oil leakage. If the air intake hose is detached or torn, foreign substances may go into the turbocharger causing damage to it. If the air intake hose is damaged, replace it with a new one. |
11. | Check the air cleaner. –
| Check the air cleaner filter for pollution state. |
–
| Check the air cleaner filter for water influx. |
–
| Check the air cleaner cover for dirtiness. |
–
| Check that the air cleaner filter is a genuine part. |
If the air cleaner filter is moistened or polluted excessively or a non-genuine part is used, intake air to the turbocharger will be reduced and the pressure in front of turbocharger will drop, causing damage to the turbocharger and oil leakage. If the air cleaner filter is moistened or polluted excessively, replace it with a new one. •
| Replace the air cleaner filter according to the maintenance schedule. |
|
|
12. | Check the intercooler hoses & pipes. –
| Check that the intercooler hoses & pipes are connected properly. |
–
| Check if the intercooler hoses & pipes are damaged (bent, detached or torn). |
–
| Check for any damage, such as crack, on the intercooler pipes. |
–
| Check that the clamps are positioned in place. |
If the intercooler hoses & pipes are damaged or disconnected, oil leakage may occur from the hoses & pipes and the turbocharger may exceed the permissible speed causing damage to the turbocharger. If the intercooler hoses & pipes are damaged, replace them with new ones. •
| Use new clamps when replacing the hoses & pipes. |
|
|
13. | Check the intercooler. –
| Check if the intercooler tubes and tanks are damaged (oil leak or crack). |
If the intercooler is damaged, the turbocharger may exceed the permissible speed causing damage to the turbocharger. If the intercooler is damaged, replace them with a new one. •
| Use new clamps when replacing the intercooler. |
|
|
14. | Check the engine oil. –
| Check the engine oil level. |
–
| Check the engine oil for discoloration, water influx and viscosity degradation. |
–
| Check the engine oil grade. |
If the engine oil level is low, amount of engine oil fed to turbocharger will be reduced causing the bearings in the turbocharger to adhere due to insufficient lubrication and cooling. If the cause of the problem is detected, add or change engine oil. •
| Change the engine oil according to the maintenance schedule. |
|
|
15. | Check the engine oil pressure. –
| Engine oil pressure: Check the oil pressure using an oil pressure gauge after removing the oil pressure switch on the cylinder block. |
–
| Check the engine oil screen in the oil pan if the engine oil level is low. Then check the injectors for gas leakage if foreign substances are accumulated on the oil screen. |
If the engine oil level is low, amount of engine oil fed to turbocharger will be reduced causing the bearings in the turbocharger to adhere due to insufficient lubrication and cooling. If the cause of the problem is detected, add or change engine oil. If foreign substances are accumulated on the oil screen, wash the oil screen and replace the injector’s washer with a new one after checking the injectors for gas leaks. Check the engine oil-related parts, such as oil pump, if necessary. •
| As the turbocharger rotates at high speed of 100,000 rpm or above, deterioration of engine oil can cause damage to the turbocharger bearings. Check engine oil for discoloration, water influx, viscosity degradation and oil pressure lowering. |
|
|
16. | Check the injectors, sensors, etc. (Refer to Engine Control / Fuel System) –
| Check that the injectors operate properly. |
–
| Check that the sensors, such as the mass air flow sensor (MAFS), intake air temperature sensor (IATS), and boost pressure sensor (BPS), operate properly. |
Improper operation of the injectors, sensors, EGR valve, etc. may cause diminished engine power. If the cause of the problem is detected, replace the related parts with new ones. |
Intercooler
Repair procedures
1. | Disconnect the battery negative terminal. |
2. | Remove the engine room under cover. (Refer to Engine and Transaxle Assembly - "Engine Room Under Cover") |
3. | Disconnect the intercooler inlet hose (A). Tightening torque : Clamp bolt : 4.9 - 6.9 N.m (0.5 - 0.7 kgf.m, 3.6 - 5.1 lb-ft) |
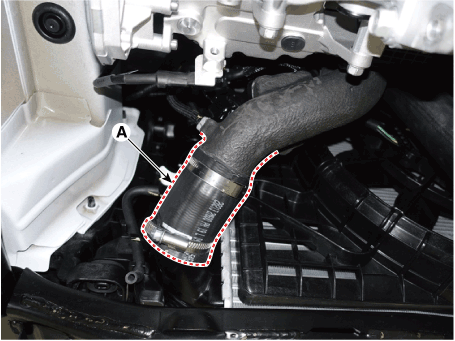
•
| Insert the hose until it reaches the end of stopper. |
|
|
4. | Disconnect the intercooler outlet hose (A). 
|
5. | Remove the front bumper cover. (Refer to Body - "Front Bumper Cover") |
6. | Remove the intercooler air guard (A). 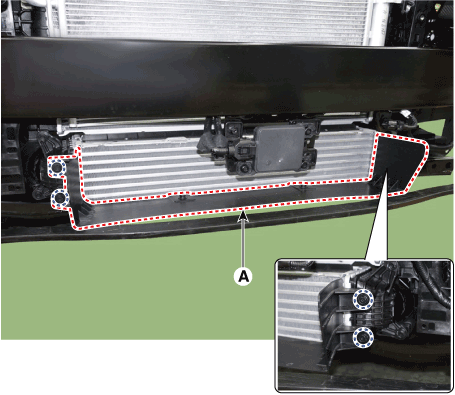
|
7. | Remove the intercooler (A). Tightening torque : 9.8 - 11.8 N.m (1.0 - 1.2 kgf.m, 7.2 - 8.7 lb-ft) |
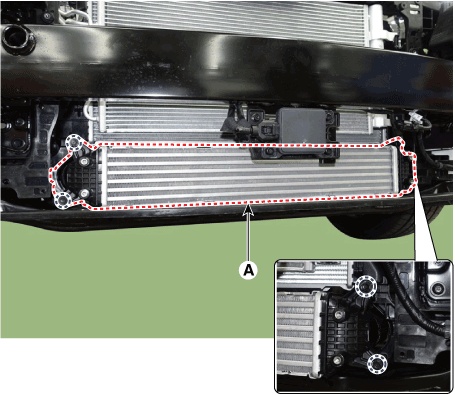
|
8. | Install in the reverse order of removal. |
Intercooler inlet pipe
1. | Disconnect the battery negative terminal. |
2. | Remove the air duct and air cleaner assembly. (Refer to Intake and Exhaust System - "Air Cleaner") |
3. | Remove the battery and battery tray. (Refer to Engine Electrical System - "Battery") |
4. | Remove the intercooler inlet hose and pipe. (1) | Disconnect the RCV vaccum hose (A). 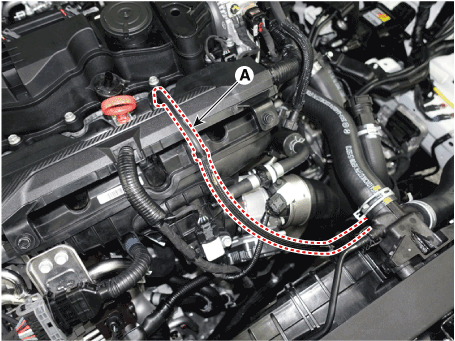
|
(2) | Disconnect the RCV valve connector (A). 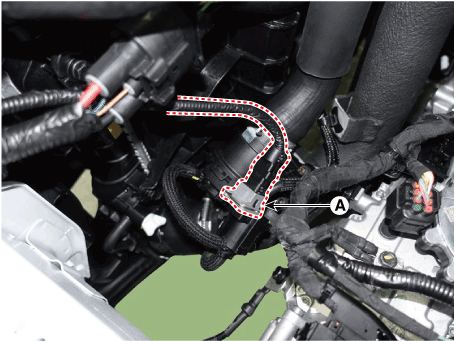
|
(3) | Remove the intercooler inlet hose and pipe (A). Tightening torque : Clamp bolt: 4.9 - 6.9 N.m (0.5 - 0.7 kgf.m, 3.6 - 5.1 lb-ft) |
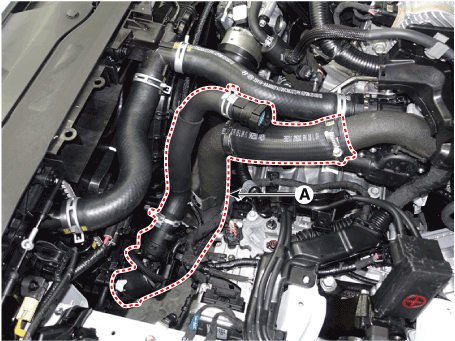
•
| Insert the hose until it reaches the end of stopper. |
•
| When installing the intercooler inlet hose, Match the alignment marks. |
|
|
|
5. | Remove the intercooler hose & pipe (A). Tightening torque : Mounting bolt : 18.6 - 23.5 N.m (1.9 - 2.4 kgf.m, 13.7 - 17.4 lb-ft) Clamp bolt : 4.9 - 6.9 N.m (0.5 - 0.7 kgf.m, 3.6 - 5.1 lb-ft) |
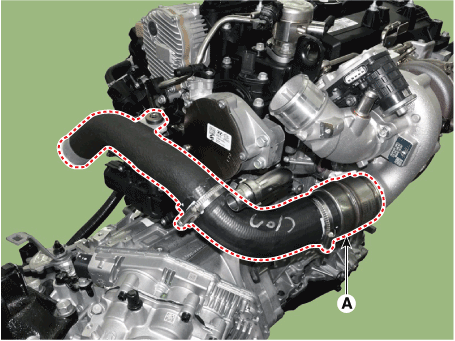
•
| Insert the hose until it reaches the end of stopper. |
•
| When installing the intercooler inlet hose, Match the alignment marks. |
|
|
6. | Install in the reverse order of removal. |
Intercooler outlet pipe
1. | Disconnect the battery negative terminal. |
2. | Remove the engine room under cover. (Refer to Engine and Transaxle Assembly - "Engine Room Under Cover") |
3. | Remove the intercooler outlet hose and pipe. (1) | Disconnect the intercooler outlet hose (A). 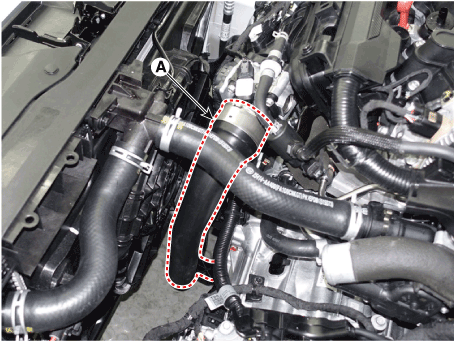
1) | When disconnecting the intercooler hose, pull the quick connector clamp (A) in the direction of the arrow as below. 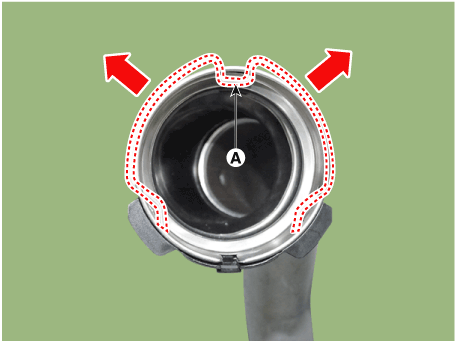
|
2) | Move the quick connector clamp from B to C position as below and then disconnect by pulling the quick connector hose. 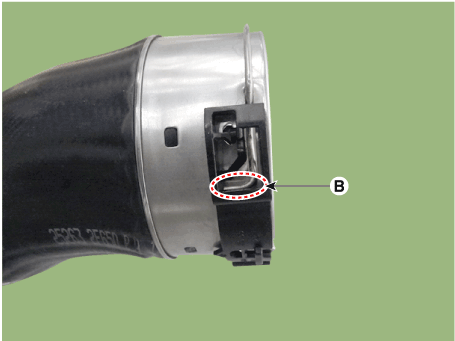
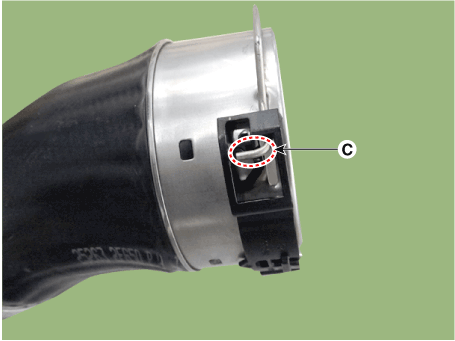
|
|
|
(2) | Loosen the intercooler outlet pipe bolt, and then remove the intercooler outlet hose and pipe (A). Tightening torque : Bracket bolt : 6.86 - 10.78 N.m (0.7 - 1.1 kgf.m, 5.06 - 7.96 lb-ft) Clamp bolt : 4.90 - 6.86 N.m (0.5 - 0.7 kgf.m, 3.62 - 5.06 lb-ft) |
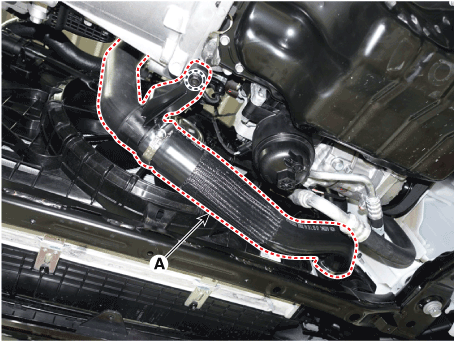
|
|
4. | Install in the reverse order of removal. |
Muffler
Components and components location
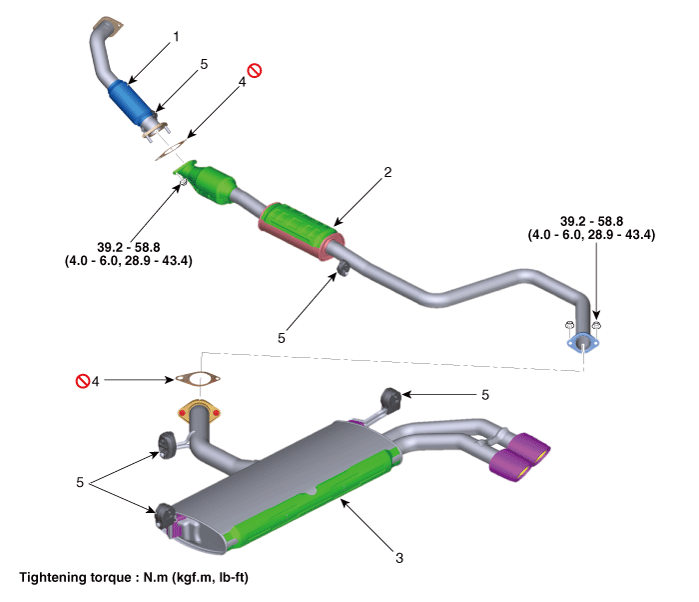
1. Front muffler 2. Catalytic converter & Center muffler 3. Rear muffler
| 4. Gasket 5. Hanger
|
Repair procedures
Front Muffler
1. | Disconnect the battery negative terminal. |
2. | Disconnect the oxygen sensor connector (A). 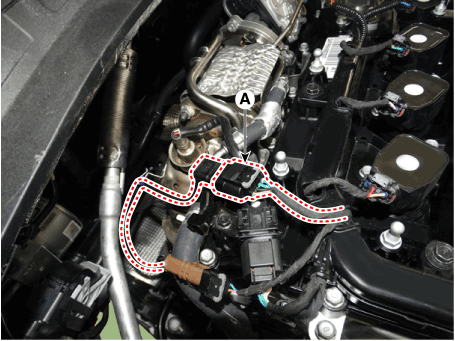
|
3. | Remove the heat protector (A). Tightening torque : 9.8 - 11.8 N.m (1.0 - 1.2 kgf.m, 7.2 - 8.7 lb-ft) |
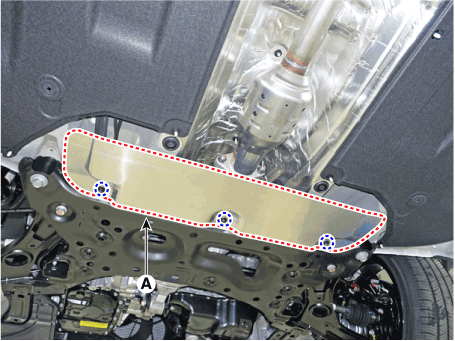
|
4. | Remove the front muffler (A) after disconnecting the hanger. Tightening torque : 39.2 - 58.8 N.m (4.0 - 6.0 kgf.m, 28.9 - 43.4 lb-ft) |
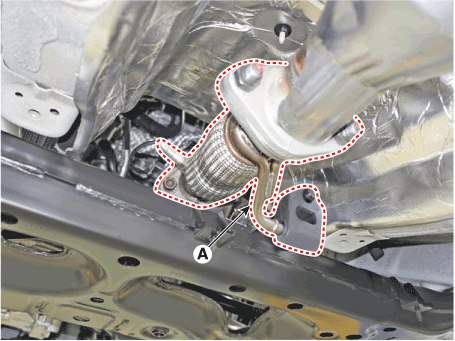
|
5. | Install in the reverse order of removal. •
| When installing, replace with new gaskets. |
|
|
Catalytic Converter & Center Muffler
1. | Remove the catalytic converter & center muffler. (1) | Disconnect the hanger (A). |
(2) | Remove the catalytic converter & center muffler (B). Tightening torque : 39.2 - 58.8 N.m (4.0 - 6.0 kgf.m, 28.9 - 43.4 lb-ft) |
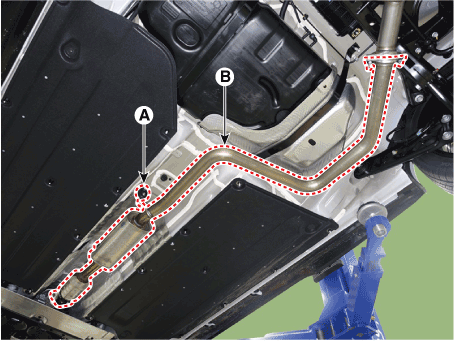
|
|
2. | Install in the reverse order of removal. •
| When installing, replace with new gaskets. |
|
|
Rear Muffler
1. | Remove the rear muffler. (1) | Disconnect the hanger (A). |
(2) | Remove the rear muffler (B). Tightening torque : 39.2 - 58.8 N.m (4.0 - 6.0 kgf.m, 28.9 - 43.4 lb-ft) |
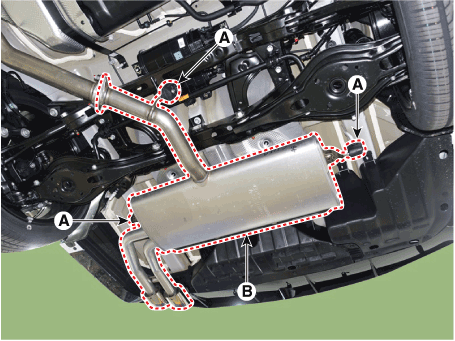
|
|
2. | Install in the reverse order of removal. •
| When installing, replace with new gaskets. |
|
|
Replacement procedure of center muffler using clamp
Under warranty : Replace the center muffler assembly.
Out of warranty : It is available to replace the center muffler as the procedure below.
1. | Check that the clamping part of the center muffler assembly is damaged or deformed. If the muffler is too corroded to clamp, replace the center muffler assembly. 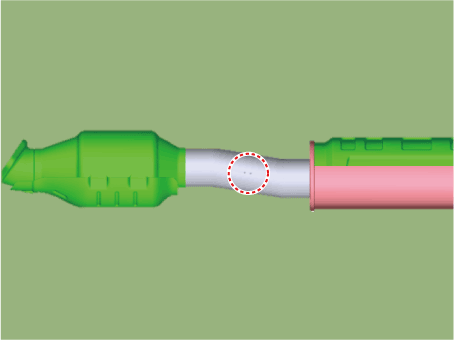
|
2. | Remove the catalytic converter & center muffler. (1) | Disconnect the hanger (A). |
(2) | Remove the catalytic converter & center muffler (B). Tightening torque : 39.2 - 58.8 N.m (4.0 - 6.0 kgf.m, 28.9 - 43.4 lb-ft) |
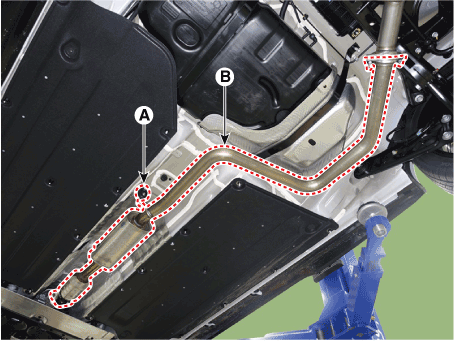
|
|
3. | Cut the center muffler as the instruction below. –
| Cut the front dent of the muffler. 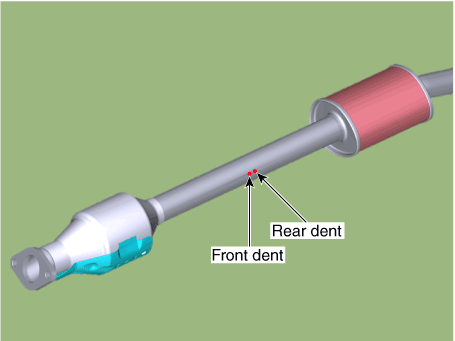
|
[A/S muffler] –
| Cut the rear dent of the A/S muffler. 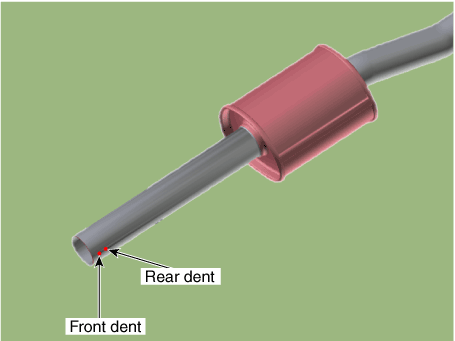
|
•
| To prevent a leak, remove the rust on the clamping part or the burr on the cutting part. |
•
| Cut the pipe vertically. |
|
•
| Pipe cutter available to cut the pipe vertically. |
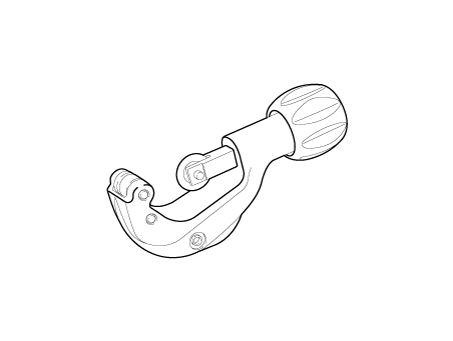
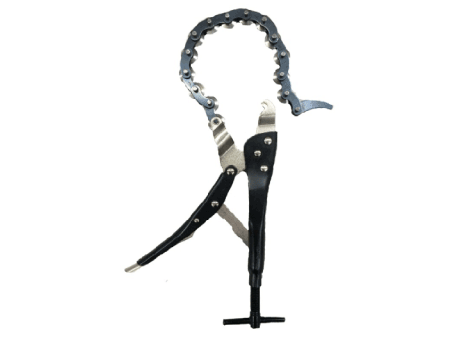
|
|
4. | Install the center muffler. (1) | Install the catalytic converter (A) and the center muffler (B) for A/S by tightening the nuts lightly, not completely. 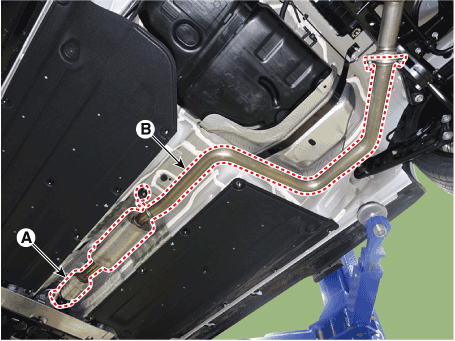
•
| When installing the muffler, replace the gasket with new one. |
|
|
(2) | Put the clamp (A) between the cutting part of each pipe and tighten the clamp lightly, not completely. 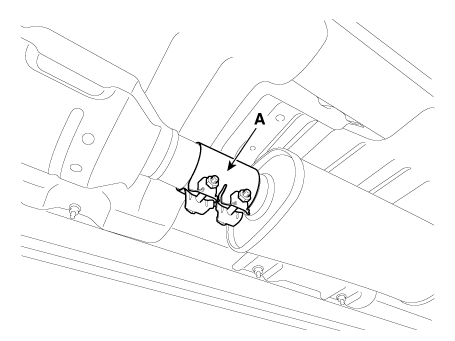
|
(3) | Tighten the catalytic converter and the center muffler with specified torque. Tightening torque : 39.2 ~ 58.8 N.m (4.0 ~ 6.0 kgf.m, 28.9 ~ 43.4 lb-ft) |
|
(4) | Compare the gap between the tail pipe(or tail trim) and the rear bumper with the record measured before removing the center muffler assembly. •
| If the tail pipe is installed differently compared to the initial position, the bumper might be damaged by the pipe heat or interfere between the tail pipe and the rear bumper. |
|
|
(5) | Do not tighten the clamp at a time. Tighten the clamp nuts to the specified torque, by turns. Tightening torque : 17.6 ~ 23.5 N.m (1.8 ~ 2.4 kgf.m, 13.0 ~ 17.4 lb-ft) |
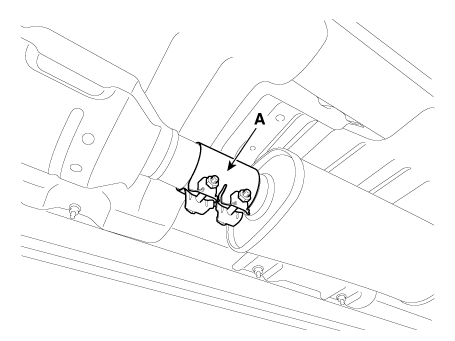
•
| Do not reuse the clamp that was tightened completely. It may cause leak to reuse the clamp that was tightened completely. |
|
|
|
Components and components location
Components1. Variable oil pump2. Variable oil pump sproket3. Oil Pressure & temperature sensor4. Oil filter5. Filter cap O-ring6. Filter cap7. Safety pin8. Oi ...